An Interview with Col. Mintzlaff
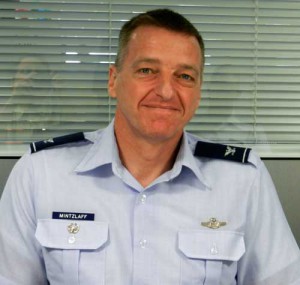
06/08/2011 – During the roundtable at Tanker Airlift Control Center (TACC) the challenge of maintaining discipline in the system was a key focus for discussion. The airlift system and the multi-modal approach reinforce one another in trying to deal with the demand side of the logistics supply chain. The predictability of this system and the performance of this system are inextricably intertwined with the demand side.
If the demander has confidence in the system, requests for supply will be closer to what he actually needs. If he does not, distortions enter the system and demand goes up significantly.
Col. Mintzlaff discussed what he called the key requirement for maintaining discipline in the system.
Col. Mintzlaff: There’s a lot of collaboration across the TACC. From the execution piece, they do all the work, and for me, the challenges are maintaining discipline in that system so that when I say this is got to move; it’s got to move. And you’ll get both extremes. You’ll get it where everything works and it moves, and you’ll get another case where it needs to move now, it’s all ready to go and in reality it may not be.
You have to maintain the discipline in the system. Is it approved? If it’s something outside of the COCOM, through OSD, is it approved? Is it funded? Is it authorized to move?
To keep discipline in that system is a challenge because airlift can often be an emotional thing. I need my “something” and I need it now. Or in the case of a humanitarian type of operation, they need it and they need it now. It still needs to work through the wickets.
Another challenge for me is maintaining a common site picture with people. I think if people understand what’s taking place at a given time, there is a logical answer to take some of that emotion out of play.
SLD: In other words, there’s a process and procedures approach
Col. Mintzlaff: Yes, there is a process and procedures approach. How come my airplane is broken for three weeks and I’m on a C5? As it bubbles up, eventually it gets to the senior. So you’re the person there to try to be the peacemaker or, you’re right, this is wrong, we need to fix it. And you go, hey what’s going on? Let’s get a plane out there, because planes eventually break.
And now, where do you make the decision to rescue it, which is a use of assets that could be applied somewhere else? And where do you say, well, it’s going to be fixed? It sounds like a clean issue, but a lot of times the airplanes are going to be fixed at noon. And then noon comes and well, no, it’s really going to be 2:00. And then maybe it’s going to be 4:00.
SLD: Or maybe ten days later
Col. Mintzlaff: Yes. Ten days later you’re going “well, when is this thing going to be fixed?”
SLD: Planning and execution are hardly the same things.
Col. Mintzlaff: I would say if everything went according to all of the plans that everybody makes, we would have the most boring job in the world. Unfortunately, all the plans that they make fall apart for various reasons. Weather affects us in various ways. Nobody can control that. You can have a crewmember get ill. Anything that delays the mission from the original plan continues to have an effect.
Aeromedical evacuation needs to move somebody right now so we need to take another aircraft out of the system.
We have many things to consider. Many times a plan will come to us. We need to do this. When we delve further into the plan we find the crew can’t do it because they don’t have enough duty day left. Maybe diplomatic clearances aren’t sufficient, depending upon where they’re coming from.
Many different pieces have to go into that puzzle. And that’s when having the senior on the floor really helps out because sometimes those hard decisions have to be made.
What are we going to stop? What are we not going to stop?
I’ve talked to many disgruntled people. “How come I’m sitting here with my C5 broken at ‘name the place’? And I’ve watched, in fact, somebody else that was on this airplane with me, another airplane came and picked them up and took them home. How come I’m still here?”
These are the situations where we tried to get it done. We were given the plan, and we worked that plan, and we worked the modifications. Sometimes we modify the modifications.
Soldiers spot a UH-60L Blackhawk while it is being loaded onto a C-5 Galaxy, Mar. 2, 2011, at Kandahar Airfield, Afghanistan. The Blackhawk upload was part of a change out; the old helicopters are being replaced by new airframes. (Credit: US Air Force, 3/4/11)
SLD: Clearly, the planning mechanisms are one thing. But it seems to me really what we’re talking about is risk management, risk communication. Trying to make hard choices.
Col. Mintzlaff: And it drives back to that discipline question. If you know you need it soon enough, you put it on a boat. We’ve made great strides working multimodally. And it helps ensure only those things that really need to be there overnight get there in time.
SLD: You’re trying to take demand off the system by moving it to the multimodal system.
Col. Mintzlaff: We can relieve some of the pressure to the extent with which we can complement our normal delivery with the ships. But the ships are going to take a longer time to get there.
SLD: You have to have metrics that give you a pretty good predictability on what you’re actually going to need. This leads to another problem, which is I’m the guy out in Afghanistan; I’m going to overbuy. Remember the just-in-time boys; how we were going to have just enough stuff and we’ll save all this money in maintenance? But, in fact, what you just described is why I wouldn’t do that; why I would buy more because I can’t rely on your air asset to necessarily be there.
And I think you probably have already looked at numbers from how much did people order in a Desert Storm versus how much they’re ordering here.
Col. Mintzlaff: It’s better now. But there’s still a ways to go. But yes, instead of ordering four, maybe they’re ordering two.
I think the point I would make was if it doesn’t need to go by air, don’t send it by air, so that if you order one, you get one. It needs to be reliable and predictable, and that’s what we’re really trying to do through the multimodal approach.
SLD: That’s a culture change for the supply chain.
Col. Mintzlaff: It is changing. You’ve gone from four or five to ordering two.
SLD: The key is as you say discipline so that there is predictability in the delivery system, and you are using air where it is most appropriate.
Col. Mintzlaff: Once you get something that’s predictable and reliable, whether it takes three weeks or it takes a day that person on the ground says it’s going to take me three weeks, so I’m going to plan for three weeks. Where it’s rough is when it’s a week, a week and a month, and he just doesn’t know.
SLD: And your point is if the part can come by sea, he’s better off having some predictability on that delivery.
Col. Mintzlaff: Or by air. Depending on what it is and when it needs to be there. If it needs to be there in 30 days, a ship might sail in 28.
I would make two points. One is if you predict out far enough, you can move it on the ship and get it there. The other piece would be the reliability part. If you’re sitting in the Philippines and you know that when you order a part it’s going to take 24 days to get there, or 14 days to get there from the time I order until I get it in my hand, then you start to build your processes around that. Where you fail is when one time it’s there in a week, or two or three times, and then it’s 24 days. Now he doesn’t know what to do. Now he’s ordering more than he needs.
SLD: So then you get distortion and behavior affecting the demand side
Col. Mintzlaff: And that’s really one of the things we’re trying to ensure, especially in this neck of the woods, is reliability. It’s going to come every so often, and plan on it.
SLD: Well, that’s very interesting. So trying to take the advantage of your fleet management interacting with a more reliable logistics supply chain management.
Col. Mintzlaff: If you’re sitting on the ground, would you rather know what you ordered is going to be there in two weeks, come high water? Or that you simply can not be certain of the delivery date? That is why we are focused on building greater discipline in the delivery system.