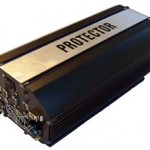
As budgets get tighter and competition among vendors accelerates, both government and Original Equipment Manufacturer (OEM) customers are looking and will continue to look for additional value from the shrinking dollars available. One way to “squeeze” more from a limited budget is to manufacture enhanced reliability and sustainability into solutions. An example of this trend is evident in the advent of rugged box-level computing systems, or “rugged boxes.” An added benefit deriving from “rugged boxes” is the ability of prime contractors to spend their focus, and the government’s money, on higher level, and presumably higher value added, system integration tasks.
Background
The term “stand-alone rugged box” refers to complete system boxes, which provide a tested and enclosed computing solution. The demand for stand-alone rugged boxes, coming from several (including the Aerospace & Defense) industries, has driven large-scale development of this technology. In particular, prime government contractors increasingly are inserting these commercial off the shelf (COTS) solutions into very demanding land, air and maritime environments.
The trend towards complete stand-alone rugged box-level systems has picked up steam. This trend has been gathering momentum in the past couple of years whereby an enclosed computing solution eliminates complex integration chores for OEM customers. As a product category, stand-alone rugged boxes today are somewhat difficult to define because they’re available in a variety of shapes, sizes and capabilities. They typically comprise a set of modular embedded boards housed in a rugged enclosure that has its own power supply and interface ports.
This new area of rugged boxes is outside the category of air transport rack (ATR) enclosures—although these continue to be a main staple in avionicsas well. The stand-alone rugged box trend also is separate from the strategy know as “appliqué,”—the term used by the DoD for its initiative under that name a couple of years ago. Appliqué involves complete computer units—like rugged laptops — that are mounted onto existing military vehicle platforms and integrated with government-furnished software.
Rugged box-level systems in contrast typically are sold as a complete working system, often with some degree of environmental testing done beforehand by the vendor. In fact, one of the major advantages of the stand-alone rugged box is the pre-testing for shock and vibration specs often accomplished by the vendor.
The system typically is designed to work as a stand-alone, plugged into whatever input/output (I/O) and user interface scheme (e.g., keyboard and/or display) meets the application need. Often the boards in the rugged box are standards-based cards such as PC/104. But the enclosures by and large aren’t in any industry standard footprint, although that may change as proposed standards gain acceptance in the military realm. Currently, there are a number of vendors that have some sort of stand-alone rugged box-level system in their offerings – many even have whole product lines.
Underlying Trends and Drivers
Much of what’s driving this trend toward rugged box-level systems comes from the current war effort in Iraq and Afghanistan. The battlefield requirement is to minimize size, weight and power (SwaP), while cramming in more computing power per watt to boost the processing muscle in smaller UAVs and unmanned ground vehicles (UGVs), as well as on larger platforms such as military vehicles, aircraft, and ships.
The proliferation of COTS products based on PC/104 standards in particular has played a significant role in the development of stand-alone rugged boxes—specifically with its modular design. The modularity of stand-alone rugged boxes provides longevity and flexibility, allowing components to be upgraded in the future without a complete system redesign – an especially attractive feature to organizations faced with tightening budgets.
Customers are not only interested in these rugged boxes as stand-alone computers, but as an upgradeable computing platform. In particular, the ability to tailor these devices with specific I/O modes has proven to be a key motivator for rapid customer adoption of stand-alone rugged box technology.
Underlying technologies Pushing Rugged Computers Forward
One of the greatest hurdles for rugged computing designers has been how to include greater processing capability with lower power consumption. Helping solve this problem has been the introduction of Intel’s Pentium M and Celeron M processors. These processors have become a popular choice for rugged systems as they originally were designed to deliver high performance with low power consumption. Initially designed for notebook computers, these types of mobile processors serve as an ideal choice for embedded computing designs.
Multi-core processing technology also is being incorporated into stand-alone rugged boxes. Opposed to one high-powered core, multi-core processors use several low-power cores that perform tasks simultaneously. This means reduced footprints, lower power and heat, and energy efficiency when compared to multiple separate CPU nodes. Additionally, Intel’s new Atom processor family creates even more possibilities for rugged stand-alone boxes.
Advancements in thermal management also propel stand-alone rugged boxes forward. Historically, numerous versions of embedded systems have been based on low-end, pre-Pentium processors, rather than on high-end processors. As a result, some enclosures were not designed with many thermal considerations in mind. However, with the advent of faster—and hotter—processors, chassis sophistication has increased to more suitably accommodate thermal issues.
Military Standards and Stand-Alone Rugged Boxes
Stand-alone rugged boxes often are tested and qualified to meet military standards, as this type of qualification testing is evidence that these boxes are being designed to the highest standards. To be truly mission-ready, stand-alone rugged boxes should at a minimum meet the military standards for temperature, shock, vibration, and ingress conditions relevant to the platform on which they will be used.
The qualification to MIL-STD-810 helps ensure confidence in a system’s ability to perform in many civil environments, including heavy machinery and mining to name a few. Additionally, many rugged box suppliers that meet MIL-STD-810F’s traditional battery of tests (temperature, shock, vibration) also will have the capacity to test the box for expanded criteria such as humidity, altitude, fungus, salt fog, explosive decompression, immersion, and sand/dust exposure — if the application so requires it.
Additionally, many of these boxes should be pre-qualified for MIL-STD-461E — electromagnetic interference/ compatibility (EMI/EMC) — and power supply operation (per MIL-STD-1275D/MIL-STD-704E) to ensure protection against voltage surges and spikes.
Trends and Drivers Going Forward
As complex computing functions increase their role in large defense programs, demand is rising for pre-integrated rugged box-level solutions. On the one hand, military programs (e.g., FCS, LCS, etc.) are becoming increasingly sophisticated and complex. On the other hand, the supply-side factor need is for manufacturers to maintain and improve profitability in a market that is, almost by definition, price-driven.
The pressure is on manufacturers to find new profit streams by adding more value, often via low level integration of functional subsystems, in response to prime contractor requirements. Key requirements for these subsystems are that they are rugged and, for all intents and purposes, “plug and play”—coming preconfigured with the appropriate hardware and software to allow them, with the addition of application software, to become productive out of the box.
The fundamental concept is that the ideal subsystem needs no further integration, validation, or testing by the customer. The prime contractor does not have to identify an appropriate enclosure or chassis, with ensuring “inside the box” interoperability, or with devising appropriate cooling strategies. That has all been done, allowing them to focus on how the subsystem fits within the broader program landscape.
The challenge for suppliers to the prime contractors is to identify the opportunity to add value — in this case, to design and develop complete, integrated, plug and play rugged subsystems that fulfill the requirement for a “black box” that takes data, processes it, and outputs information. The prime contractor’s responsibility for the subsystem would end, in effect, with getting an input into the box, and begin again as the information comes out of the box. The key underlying task for vendors desiring to be leaders in defense market rugged box production therefore is to identify the “silver bullet” applications where the design, development and manufacture of a rugged box would add the most value for the prime contractor in the way described above.
Rugged Boxes and the Future
Rugged boxes are not new. What is new is the accelerating rate at which they are entering the military market, driven by the needs of the prime contractors to focus on their key value added roles, eliminating time and effort spent on lower level tasks.
These boxes answer the needs created by the increasing sophistication of military applications, in turn driven by the network-centric nature of the battlefields of the future. They also answer the supply-side need of vendors to add value in a marketplace that, by definition, is often price-driven.
Rugged boxes’ future roles depend on rapid advances in embedded computing technology, which are enabling ever higher levels of functional integration on the computer board. When combined with advanced cooling technologies and sophisticated rugged designs, these new boards enable flexible high performance by small, low-power, lightweight rugged subsystems, integrated in a way that was inconceivable only a few years ago. They hold the potential for easily upgradable, “plug and play” functionality for both OEM and government customers, thereby providing an enhanced level of reliability and ease of maintainability. For the defense industry it looks like rugged boxes have a future.
———-
***Posted September 4th, 2009