2015-05-29 The Marines are the core customers for the V-22.
And no military force in the world is more demanding of versatility than the USMC.
A good example is how the Marines have driven multi-mission capabilities from their KC-130Js with the harvest hawk system.
Here the tanker/lifter becomes weaponized and capability of shaping mother ship C2 capabilities.
And the versatile C-130J can with various roll-on-roll-off capabilities play an even more flexible set of roles going forward.
Lockheed Martin has evolved the C-130 to be able to provide a range of capabilities ranging from medevac, to ISR, to C2, to weapons delivery.
As Lockheed Martin puts it: “Buy a C-130 and get an Air Force.”
The Osprey is now going down this path.
And because of the capability of the Osprey to operate virtually anywhere, this means that multi-mission can be provided via ship or land bases, or at virtually any point of attack.
The V-22 can perform in the heart of the flight envelopes of both conventional helicopters and fixed wing turboprop aircraft, providing the flexibility of both capabilities in one aircraft.
The Osprey has redefined assault forces, and has led to the creation of new approaches to amphibious assault.
Now with multi-mission capabilities becoming available, the range of capabilities available to the assault force is broadened.
This is particularly significant as the amphibious strike force is redefined and able to carry organic capabilities hitherto only available to a large deck carrier.
During the visit to the Boeing V-22 Osprey plant at Boeing’s Philadelphia site, the Boeing team explained the range of possibilities for the Osprey adding multi-mission roll-on-roll off capabilities.
In the slide below the core capabilities being worked are highlighted.
Indeed, an example of the flexible uses of the V-22 were illustrated during the USS WASP-F-35B integration tests
The F-35B engine is modular, and the Osprey brought the largest module directly onboard solving any question of supplying engines for the F-35B underway on a large deck amphib or carrier for that matter.
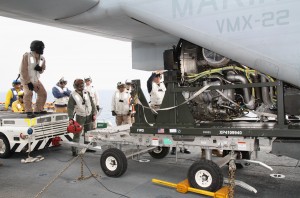
What is being worked in the near term is the aerial refueling piece.
The USMC clearly wishes to add aerial refueling to its Ospreys to work with the F-35Bs and Harriers aboard their large deck amphibious ships.
Obviously, this adds organic capability, which expands the initial insertion options for the USN-USMC team. It also opens up possibilities of change for the large deck carrier community as well, both US and worldwide.
The capability is important, but equally interesting is the approach Bell-Boeing has developed to prepare for the possible introduction of air refueling.
During the visit to the factory, a visit to the multi-mission lab and a discussion with Ted Bayruns, Associate Technical Fellow and V-22 Modernization Lead Engineer, highlighted the very innovative approach being taken.
Basically, through the use of a 3-D Virtual Reality simulation facility in which human operators are inserted during requirements definition, the process of shaping an onboard aerial refueling system is crafted whereby adjustments can be made early to the system to optimize it in terms of potential operator use.
This means that validated requirements can feed to the preliminary and detailed design phases.
Continuous use of the lab throughout the remaining engineering development tasks supports “in-process” evaluation of prototypes which are incorporated as requiredto the baseline. Instead of taking years, months are required to get an initial design right.
During the visit, Douglas Fischer, Boeing V-22 Lead Human Factors Engineer, described how Boeing is using virtual reality to reduce the engineering cycle time, reduce program cost, and improve system integration.:
Boeing Philadelphia has used virtual reality for years to support a variety of projects and programs, but primarily for concept development and design reviews.
We are now developing tools and capabilities with the VARS program to use virtual reality technology within the systems design engineering model.
The traditional systems engineering model completes processes such as requirements development, design definition, design reviews, testing and verification in a sequential manner.
Using a virtual reality rapid prototyping model allows us to simultaneously conduct the systems engineering processes.
This means we are able to support concept development, requirements verification, design reviews, and testing processes at the same time.
And then we can not only develop a workspace that’s suitable for the operators, but we can also start developing installation procedures and maintenance tasking.
The modification to our systems engineering supports rapid decision making and eliminates integration errors, reduces program costs, and enables us to support accelerated schedules for the USMC.
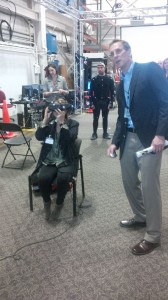
And Fischer underscored that working with real world operators was a key part of an effective process.
We work directly with aircrew members to fully develop a design that satisfies operational requirements.
Use of the virtual reality capabilities and 3D modeling adds a new dimension to our design process and greatly enhances our discussions with our operators and customers.
The aircrew members are able to look at the designs in this virtual environment, and thoroughly understand how we are integrating our design concepts.
With their participation are able to assess operator functions such as line of sight, physical reach, and maneuverability within the cabin with this virtual structure in place.
We’re able to make changes based on their operational description and their movements within the cabin, and how they’re going to use the system.
And then we’re able to make real-time changes with the operators so that the design best fits their needs.
He then discussed the approach to where to place the control panel for the refueling process and through the approach taken, they ended up moving the control panel significantly within the simulated cabin to improve operator performance.
And all of this is being done prior to building the actual system.
And another benefit is the ability to look at the impact, which any modification might have on the aircraft for the overall performance of the aircraft itself.
Fischer added:
Clearly, modifications have an impact to wiring, structure, payloads, and other engineering teams.
What we can do is bring all of the concurrent engineering into this lab and be able to verify that the proposed design changes are not creating a new problem for the aircraft.
Bringing the con-ops into the design process is also an advantage, which can be facilitated by the new approach.
Fischer concluded:
We weren’t really sure how they were going to use this tanking equipment, so we brought out our operators and air cabin and aircrews, and we developed the CONOPS with them.
We’ve never done that in a design review or technical meeting before.
We’re actually able to come here, immerse the operators in the virtual environment, and go step-by-step through the procedures, and identify, add, delete, the procedures based on their inputs on how they’re actually going to use the equipment.
This approach provides a unique and informative understanding of whether the proposed concepts are usable and allows the operators to complete their jobs.
We don’t define our customer’s requirements and conops…we invest to mature potential capabilities.
In other words, the Osprey is entering the next phase of its development, a multi-mission phase.
And with that evolution come new tools to shorten the development time to introduce the new capabilities.
This is the third piece in our Osprey series.
For the first two pieces of a six part series see the following:
https://sldinfo.com/osprey-at-the-eight-year-mark-preparing-for-the-next-phase/
The visit to the Boeing facility was done by Robbin Laird and Murielle Delaporte, with Delaporte’s pieces to appear in the French press later this summer.