Much lost in the U.S. scurrying for dollars in dealing with “overseas contingency operations” and paying for the Obama “stimulus package” and “health care reform” is the significant question of the role of manufacturing in the evolution of the U.S. economy and its global competitiveness. Notably when President Obama delivered his major address on science to the National Academy of Sciences, defense and aerospace were relevant only as historical examples, rather than as critical elements of shaping future capabilities.
Yet for modern military forces, the question of the “manufacturability” of defense goods and capabilities is crucial in the operation and deployment of a global force. Indeed, one could argue that those failures of acquisition which have happened since the early 1990s in the United States have been largely been rooted around pursuit of well-designed briefing slides rather than well-designed manufactured products. The difference between the debacle of the Future Image Architecture and the F-35 could not be starker. Whereas the failure of FIA has left the United States with a significant intelligence gap, the core focus on the F-35 program has been on manufacturability and this includes how the systems on the aircraft will operate as well to allow the aircraft to operate as a “flying combat system”
The F-35 is a 21st century manufactured product which embodies capabilities similar to the new manufacturing systems used by Boeing and Airbus in producing their next generation commercial aircraft.
The F-35 is not a traditionally produced combat aircraft, which is assembled from a myriad of components provided by suppliers. It is a moving-line high tolerance manufactured product in which system providers operate as key partners manufacture assemblies and sub-systems. Stealth is a product of the high-tolerance manufacturing process, and not crafted in by essentially hand-built efforts.
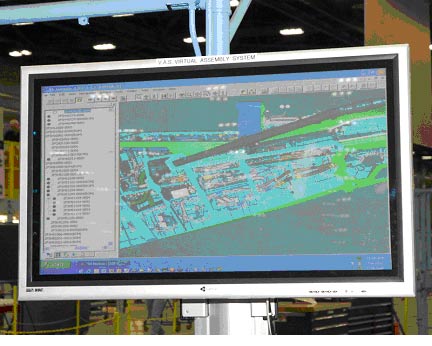
As a program, F-35 has been built around new manufacturing processes. These processes are an essential part of the systems development phase or SDD. In this process, the machine tools and various elements of the production process are being pre-tested through the actual production of test aircraft. Based on feedback from this process, the machine tools and various elements of the production process are being altered so that when full-scale production comes it will be as efficient and effective as possible.
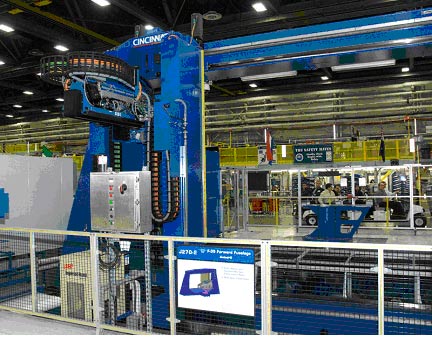
The F-35 approach is embodied in the concept of an advanced Fighter Production System. FPS is a 21st century manufacturing approach in which the final assembly facility is the outcome of a closely networked system of global suppliers.

The engineering approach underlying the manufacturing system has closely linked the core stakeholders in the production process from the start. The collaborative process has been designed to ensure that a high-tolerance manufactured product would emerge, rather than having a traditional supply chain whereby the flow comes from the periphery to the final assembly center.
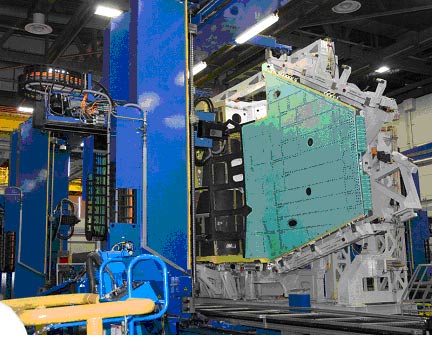
The F-35 is a hub-and-spoke system whereby the collaborative information sharing and engineering processes are co-located in the hub but closely connected to the stakeholders. A digital thread manufacturing capability enables the collaborative system.
In Digital Thread manufacturing the CATIA computer model feeds directly into a Computer Numerically Controlled (CNC) machining center, and CoordinateMeasurement Machines (CMM), or is processed in a Composite Programming System (CPS) before being sent to the Fiber Placement Machine. In both cases the finished product can be traced back to the original computer model through a “digital thread” which ensures greater precision and accuracy in manufacturing.
The F-35 is a globally sourced product. The global sourcing is based on the basic manufacturing model for the F-35. Global suppliers are stakeholders in the digital thread manufacturing process and collaborative participants in a networked engineering approach to the development and production of the aircraft.
The cost of aircraft produced by a 21st century manufacturing system will be driven down by the automated nature of the production facility. At the height of building the F-16, 18,000 persons were necessary to produce the F-16 on the final assembly line. For the F-35, 3,000 persons will play a similar role. The number is significantly reduced on the final assembly line in part as well to how the process works in using already assembled sub-systems which the final assemblers then integrated into the aircraft. The cost of a 21st century combat aircraft of the new generation is driven down and maintained by a new generation approach to manufacturing.
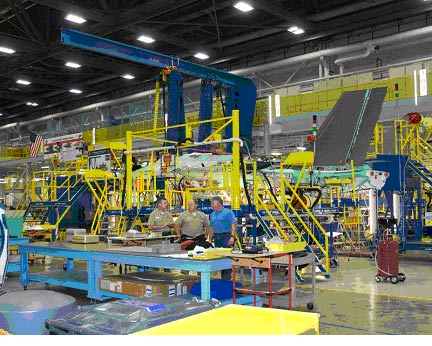
An example of the different quality of the man-machine relationship in the F-35 program compared to other aircraft is in the process of making the F-35 a stealth aircraft. Stealth is a result of a high tolerance manufacturing process, and not a handcrafting effort. The final coat placed on the aircraft is a robotic coating process. The tolerance for the final coat on a F-35 is the size of a human hair, which would not be possible except through a robotic process.
And repair for the F-35 in the field will be provided by a common set of tools and systems, which all the partners in the program acquire along with the aircraft. At the Fort Worth facility of Lockheed Martin, a low-observable repair facility is in operation, which involves shaping the proper tools for doing stealth repair in the field. Partners in the program visit the facility regularly and are part of the test program to determine how best to maintain low-observable aircraft in the field.
And costs are further reduced by the logistics and sustainment capabilities built into the F-35 as a manufactured product. The aircraft has been designed with manufacturing and sustainment considerations built in. Several of the tools being used to build the aircraft will be the same tools used to maintain the aircraft. The high degree of automation built into the integrated sensor systems on the aircraft will allow real time monitoring of the state of health of the aircraft, and this data will be delivered to the logisticians in real time. Such data will be useful both for more effective operational and combat considerations, but will drive down maintenance costs on the aircraft. The cost of weapons support to the aircraft is driven down as well by the reduction in staff necessary to weaponize the aircraft on operational assignments.
Also, the way the supply chain has been set up will allow the sustainment system to operate more effectively as well. The manufacturing team for F-35 works on an aggregated demand model whereby one set of priorities is established between the prime and the suppliers. This set of priorities encompasses requirements for sustainment and production, rather than treating these as separate processes.
Another aspect of the manufacturing process central to the F-35 is the AESA radar and integrated sensor systems on the aircraft. The nature of these integrated systems shapes the concepts of operations of the aircraft and the ability of the aircraft to operate as a “flying combat system” able to shape air combat as well as air-surface operations.
The manufacturing process underlying this capability comes from Northrop Grumman’s Electronic Systems production facility in Baltimore, Maryland. Here the core reality of this production system is the production of small radar chips which function as radars in and of themselves, which are then combined in a variety of platform products. These chips are produced by a highly automated production process, which reflects several years of manufacturing experience, so that the F-35 systems, which are built around these chips, are inheriting the experience of several legacy platforms.
Although central to the F-35 enterprise, the new manufacturing approach is not widely appreciated. The next three years of funding for the program provide essential funding for ramping up the capability to launch production. Although the program is expressed in numbers of aircraft, for the next three years the numbers of aircraft are more significant as generators of revenue to prepare for LAUNCH of production. Much of the program money for the next three years will be pushed into the stakeholder manufacturing base to build the appropriate machine tools, carbon fiber thread machines, and related manufacturing systems and assets.
In short, the F-35 is an example and certainly not the only one of a significant advance in manufacturing technology and production approaches and processes. Recognizing the significance of these capabilities to the United States and its allies is an important strategic requirement for the decades ahead. Although “cash for clunkers” might appear to be a useful addition to the U.S. defense supplemental, it would be more credible if U.S. leaders would recognize the risk to the nation and to its allies of losing its edge in the manufacturing base.
The author visited Lockheed Martin production facilities at Fort Worth in December 2008 and July 2009 as well as Northrop Grumman’s Baltimore manufacturing facility in July 2009 in writing this story. The pictures included in the story were taken in December 2008. A version of this post will be published in RUSI Defence Systems in 2009.
———-
***Posted August 12, 2009