2013-07-24 Recently, the F-35A maintainers received an award from the base command which highlighted their progress for the past year.
According to a press release (July 17, 2013) from the 33rd Fighter Wing:
The F-35 Joint Strike Fighter program continues to garner accolades, as the 33d Aircraft Maintenance Squadron won the 2012 Air Education and Training Command Maintenance Effectiveness Award for the past year.
The award is given to a maintenance unit for mission accomplishment, effective use of resources, innovative management practices and quality-of-life programs. The squadron was measured against other legacy fighter units.
The unit led the way by accomplishing a number of program firsts, such as executing the first operational F-35A mission and graduating the first F-35A non-test pilots. Flying wasn’t the only focus as personnel also benchmarked training syllabi, established maintenance practices and verified tasks used by all future F-35 maintainers.
The squadron performed these and multiple other tasks while exceeding flying and scheduling effectiveness standards, as well as garnering an “excellent” rating during the unit’s first compliance inspection.
This is a major command level award to the unit.
We had a chance to talk with some of those maintainers about the progress over the past year and the way ahead. Three maintainers participated in the discussion: Lieutenant Colonel Maurice Lee, the commander of the unit, Master Sergeant Ted Hackler, and Technical Sergeant Dustin Ossman,
The wing currently has 12 F-35As with more on the way. The team is working on a variety of LRIP airplanes and shaping a common maintainable aircraft for the wing.
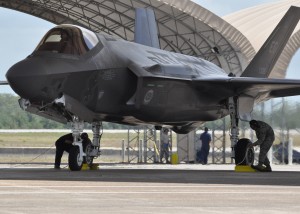
SLD: What has been your focus for the past year?
Lee: Iin the past year, we’ve been developing our maintainers as well as the aircraft to be able to fly the aircraft safely.
Hackler: We are training air force pilots and maintainers to plant the seeds at our future bases: Luke, Hill, and other future F-35 units.
SLD: What is your background? What planes did you work on previously?
Hackler: Originally, I am an F-35 avionics maintainer. I worked the 16s for about 12 years. I worked the Osprey for about two years, and I’ve got almost three years on the F-35. I’ve been to Pax. I’ve seen how the Navy does business. I’ve been to Edwards. I’ve seen full test world, and I’ve been heavily involved in the avionics here at Eglin.
SLD: What’s the biggest difference between the 16 and the 35 in your avionics maintenance world?
Hackler: I would say it’s going from like a 1990s car to a 2000s car.
With the technology that we have in these aircraft and the systems that we’ve brought on line, it’s greatly enhanced our capability in the field to provide our pilots.
It is exciting to see the new systems on line because they’re bringing new capabilities and better imaging, better range to the pilot.
SLD: Could you provide a sense of what your last year has been about and what the award recognized?
Lee: We have had aircraft flowing in during the past year. And then for a period of time, we have worked with the two different maintenance systems, ALIS 102 and 103, The first big challenge is loading the aircraft and getting all the records into ALIS.
On the aircraft side is getting all of the scheduled upgrades to that aircraft because every time we get a new batch of airplanes, they’re going to be either one block or the other, and of course that changes as LRIPs come in.
The most current airplanes that we have are 2A. Some of the original aircraft that we had were 1A aircraft and then we ended up upgrading those aircraft to 1B configuration due to some software and hardware upgrades.
The big challenge is to keep all the aircraft configured the same way. We went from 1A, and then we had all aircraft upgraded to 1B, and we have delivery of some 1B aircraft, and now we’re getting 2A aircraft.
Each iteration brings with it more capabilities than the way of the avionics systems that Master Sergeant Hackler was talking about.
We are folding in the DAS and ETOPS capabilities now.
But one has to realize these are software upgrades so it is a question of loading the software and ensuring continuity across the aircraft.
You are uploading software.
Over the past year, the transition to ALIS 103 has been the big challenge, as well as getting the technical data for the maintenance regime validated as we go ahead and gain experience.
Recently, we added another capability, namely being able to do hot pits. This is having the aircraft running, putting gas on, and getting another sortie rom the same aircraft. We have now incorporated into our weekly flying schedule.
SLD: You are working to shape the maintenance regime for the first IOC aircraft which deploy as a squadron for when the squadron deploys the aircraft is common and the maintenance regime is common. So you are working towards that goal?
Lee: That is the focus. We took at the beginning of the last FY a cadre of maintainers that were experienced already on different aircraft. Now those can be anywhere from the F-15, the F-16s, we have guys here from U-2, so what we’re building a training plan for the avionics career fields that incorporates all of the aircraft systems.
As we turn on systems, we’re getting to train on those systems at the same time.
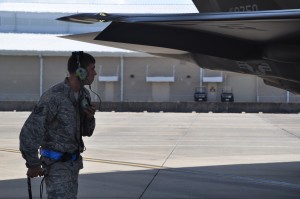
In a classic developmental test world, what you would do is you would have aircraft flying in test missions every day with test points and it’s a very, very deliberate process every day. And you know guys sitting in control rooms looking at the data, looking at everything like that.
What we’re doing here as we upgrade those systems and have those training plans, those are moving and being developed at the same time for what we call concurrency. So, as we move rapidly through those things, we’re trying to keep up with our documentation and training at the same time, which makes it a challenge but also puts things in the field a lot quicker.
Again, it is about software upgrades; when the testers approve the software, we upload it and then use it. That really is the meaning of concurrency. It is a big word for a straightforward process.
SLD: We have talked about software, but obviously you are working the hardware piece and determining how most effectively to work with the new hardware as well.
Lee: We are. For example, we’re talking about a new concept for the engine built around module changes, and a lot of new airframe type things with developmental of everything from the wheels all the way up, airframe, substructure, and different more enhanced low observable maintainability. We’re touching all those pieces too in shaping the maintenance approach.
SLD: Could you outline your approach to maintaining the engine?
Lee: Once we have an engine change at a classic engine shop, you have an engine shop that would tear down the engine down to the individual fan blades, stators, rotors, and everything, combustion cans, etc.
What we have here is a different approach.
If the engine is bad, let’s say, you take the engine out and you send it to the back shop here. The back shop here has the capability to change modules, which is the fan section of the engine, if you will, not the the front half with the turbine and the fan.
If it goes any deeper than that, we send it off base back to the contractor who’s on contract to provide the level of service and a spare so that our readiness level stays at a certain percentage. We’re still working through that.
But as it stands right now we’re not looking at having heavy type overhaul maintenance residing on each base.
The bases will have the capability to change out modules and replace parts but anything heavier than that will be handled elsewhere.
SLD: This clearly can affect you know the size of the maintenance pool that you’re going to have on base to maintain engines, for example. It’s going to affect not only the approach but the manpower approach that you’re going to take to this as well.
Lee: That is correct. It is a major change. For example, you’re going to have a lot less people in the engine career field, and they’re actually combining them with crew chief career fields.
Ossman: Let me comment on this change. Crew chief, mechanic basically, they’re combining both of us with an engine guy and crew chief. A crew chief basically maintains the aircraft, and does hydraulic work, and does some engine work, but normally at a legacy base you’d have an engine guy that’s all he dealt with was rebuilding engines, removing them. But we are getting a lot of engine guys coming in and combining career fields and it’s working out pretty well.
Lee: We have a whole shop dedicated to the low observable systems on the aircraft, the coatings etc. We don’t do those. We are talking about the other airframe type issues: changing tires, changing brakes, performing the pre-flights, getting the aircraft ready to fly, changing out filters on the engine – those kind of things that we’re talking about.
SLD: The F-35 is part of the 21st century approach of designing for maintainability. How has the design of the aircraft changed your jobs and made them different and easier?
Hackler: When you look at the legacy fighters, we had big boxes inside them. This has changed along the lines of what we have done by having smart phone.
We have been able to decrease the size of what’s required to run a certain system. So, we’ve been able to turn it into cards or something smaller where we and don’t need to have a huge system to back it up or provide that type of power that we used to on Legacy Fighters.
SLD: And removing things like significant reliance on hydraulic systems is a big change as well.
Ossman: It is a big change. I work in that area of expertise. The F-35 like Master Sergeant Hackler is talking about are fly-by wires all fifth generation; a lot of the hydraulics that are in a legacy aircraft have gone away and most of the actuators were self-contained like reservoirs, so you don’t really don’t have any bleed issues or hydro leaks or anything like that.
For us, it’s a lot simpler maintaining the plane.
I come from an F-15 background. And hydraulic issues are common. There are a lot of times that you had hydraulic leaks and the jet would be down for at least a day. When you come to an F-35, it’s fly-by-wires, so you don’t have all the hydraulic lines running through the aircraft, so less opportunity for leaks or something chafing in and blowing out in flight or something like tha.
Obviously, this improves our mission impact and be able to produce more sorties because you have less hydraulic issues.