The View from Pax River
07/18/2011 – In mid-June, the Second Line of Defense team visited Pax River and received overviews on various aspects of the test program. One of those aspects was shaping the maintenance approach.
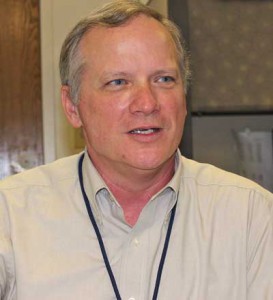
During our visit to Pax River, Second Line of Defense sat down with Craig Paramore, the Lockheed Martin Flight Test Control Engineering (FTCE) and Autonomic Logistics Information System (ALIS) Integrated Task Force (ITF) Lead within the F-35 JSF Integrated Test Force at Pax River.
SLD: Could you provide us with a sense of your background and current role in the program?
Paramore: I’m a flight test control engineer, and retired USAF MSgt, F-16 Avionics Craftsman. My computer background led me into the ALIS world. Right now I’m one of about two people outside the Orlando development team that holds admin rights to the system from LM Aero. There are only two of us that I know of that have admin rights inside the computerized maintenance management systems.
I’m, “quote,” an ALIS subject matter expert for Aero as well as my front line is controlling the airplane like a Production Supervisor for the airplane. We control and coordinate all the engineering interfaces to the aircraft and maintenance.
In other words, we are the central point of focus for that airplane for any engineer that wants to work the airplane, for any engineering direction to the airplane, for request for engineering from the maintenance crew, as well as helping maintain the configuration management of the aircraft.
That’s what a control engineer does on a daily basis
SLD: Have you done this for Gen-4 aircraft at all?
Paramore: I have done control engineering for Block 60 aircraft; and then transitioned straight from Block 60 F-16 for the UAE to the F-35 program.
The Block 60 was the most advanced F-16 ever built. Avionics-wise, the airplane was called an F-16 because the airframe, basically, didn’t change.
They beefed it up in areas, but the biggest changes were the avionics packages, and being an avionics technician by trade I saw those every day. I see a lot of that similarity and beyond now in the F-35 because it’s even more advanced. Block 60 doesn’t compare in our world today to the F-35.
SLD: So what’s the difference between a Block 60-enabled F-16, which is the most advanced F-16, built today and an F-35 from this particular avionics point of view?
Paramore: The maintenance concept, when fully matured it is going to be something that we’ve never had the pleasure of before. F-22s, I know a little bit about, I have friends of mine that have been on the program and actually are maintainers in the field for the F-22. Those guys tell me about how easy their aircraft is actually from a maintenance perspective.
This is going to make it even easier from a maintenance perspective because of the way our maintenance concepts are set up on the F-35.
SLD: But at the end of the day, from your point of view, even before there is a fully matured maintenance regime, and the first batch of aircraft are delivered, how will the maintenance approach very, very different from a 16?
Paramore: On a F-16, for example, all your actuators are still hard-lined into the hydraulic system. The actuators on the F-35 are fully self-contained: four cannon plugs, some bolts, and it pops right out after you take your panels off.
On the F-16, you’d be four cannon plugs, eight bolts, two hydraulic lines, refuel or resetting the hydraulic systems, re-servicing those, bleeding and leaking them, and then doing the ops checks, not to mention if you had some kind of rigging you had to do for the actual actuator if it wasn’t just a straight swap, you’d had to go in and do all your rigging for that actuator. The F-35 system self-adjusts the flight controls, so once you go in and replace an actuator, you run auto-rig, and the system auto-rigs the actuator.
SLD: So, you get two immediate benefits. One is you’re talking a much shorter amount of time necessary to get the plane airborne, which gives you the second advantage which is you get a better sortie generation rate out of the same aircraft, better use out of the aircraft.
(Click here to read a discussion of the actuator system.)
Paramore: Absolutely, and also, your follow-on maintenance is going to be reduced because of the auto-rig function, for our actuator example. It’s a software auto-rig, where the F-16 was a mechanical. You had to have people out there with rulers, turning nuts and bolts to adjust the actuator. The other thing is that you don’t have to hook a hydraulic mule to this airplane once you remove and replace the actuator. That mule is not required because the unit is all self-contained.
SLD: What’s a mule?
Paramore: It’s support equipment, the official name is ground hydraulic cart.
The endgame for the F-35 is for the aircraft to report back to the ground before it ever comes back. Let us go back to our actuator as an example. If you have a hydraulic actuator that’s starting to need replacement, let’s say the fluid level starts to deplete for any reason whatsoever, the system will detect that trend, report it back to the ground, and through that reporting, you start looking at the electronic data, you can determine when that EHA will have to be replaced. You can also have the CMMS system, and the PBL (Performance Based Logistics) system; identify a need to get one shipped to the site for replacement on that airplane.
SLD: And the technological opportunity inherent in this process, if one take’s advantage of it, should allow the system to handle the supply chain differently, should allow the possibility of swapping parts at bases, and all for cross service and cross national sharing when possible.
Paramore: Yes it allows for that kind of “sharing”. The technology is driving a lot of everything, including maintainer mind-think, as I like to call it. If you come in here as an old hat maintainer, and you’re stuck in your old world of documenting maintenance, for example, then you’re already going to be behind the power curve because this system does not afford itself to old hat thinking.
You have to open your mind up to a new way of doing business. When I was in the Air Force, we had five standard priorities for ordering parts. For example, I’m ordering this priority 5 or I’m ordering it AOG, which is number one.
In our system, we have two. It’s either AOG or its routine. And that’s because the metric is 72 hours standard. If you order anything on routine, the business model for this is we should have that part here on-site within 72 hours. If it’s truly stopping you from flying an airplane, you put it AOG and it will be next flight out from the warehouse location.
SLD: What does AOG stand for?
Paramore: Aircraft On Ground. In other words, for the Air Force folks, that’s a MICAP, Mission Incapable. You’ve grounded the aircraft.
The system is tracking parts to determine the life limit on the part as well. The system tracks these in a visual system queue. The item will move up a list. Basically Squadron Health Management (SHM) says your part is coming due for change.
(Click here to read a discussion with a USMC maintainer of the F-35.)
The test version of the laptop to be used as part of the maintenance management regime on the F-35 (Credit: Lockheed Martin)
SLD: A key impact of the F-35 is to reduce significantly the amount of touch labor necessary to operate the plane. The USCM, for example, expects at least a 30% reduction in touch labor. Why is that so hard for people to grasp and to understand that this will lead to significant cost savings?
(Read here General Trautman’s discussion of the change.)
Paramore: My personal opinion is that the reason it doesn’t appear is because people – and bureaucracy in general – don’t like to see the human factor go away. They like to see a stable workforce. When in reality, we’re helping the economy by reducing the manpower effort on a smart airplane. And that’s what we have is a smart airplane.
SLD: And I think we’re confusing touch labor hours with manpower. You really want to put your manpower into an optimal support function. It’s not just measured by number of touch hours.
And the shift from paper to digital will have a significant impact as well. Maintenance manual, the old cards, QAs, you know the approach. Will there still be a big maintenance manual sitting around? Do you still need that analog?
Paramore: No. Actually the air system that’s being developed will shift this paradigm. It is not just an aircraft it is a new air system.
Performance-based logistics system, the maintenance management system, the supply chain system, and the tech data system are all parts of a new maintenance paradigm.
The tech data system – joint tech data is what it’s called, or JTD – is all electronic. This whole system is logistics control number based. If you work on an F-16 or an F-15, then you’re familiar with what’s called the MIDAS system, which is system, sub-system, sub-sub-system and then task number ID.
Same sort of concept applies, but not to that same flow. Theirs was a strictly logical LCN structure, if you will. The MIDAS system was basically lined up with all parts of the system shown in the system structure.
The F-35 system is a physical structure, which says if you have a hydraulic part attached to an engine, you’re going to find that part under the engine system LCN tree, not underneath the hydraulic system because it’s attached to the engine. It’s a physical structure.
SLD: It’s a function of being part of the engine.
Paramore: Right. But the system is still the same. You just click a link to your joint tech data; you search down and say I want to remove this hydraulic pump. You find the LCN for the pump in the tree and you go click, and it opens up, and it has all hyperlinks to your input conditions.
It will say that you must take this panel off. You must de-service hydraulics. Whatever is required, it tells you in the input conditions, and then it goes through all the steps just like a regular job guide did, under the MIDAS system.
SLD: Would this be a hand or a laptop computer operating the software?
Paramore: It will be on the PMA (Portable Maintenance Aide). Basically, it’s a rugged laptop. In the next version of ALIS that we’re releasing this fall, you’ll be able to sync the PMA to the ALIS system. You will tell it what jobs you’re working, pull them over to your laptop, and it has the JTD already stand-alone on that PMA as well.
SLD: So now I’m flying back. I’ve done a mission, and I’ve expended my ordnance and returning. Something is not synced. I’m flying into the base. You guys already will have a signal from the airplane into the whole data-linked network of maintenance supply — how then does that process work?
Paramore: The system (aircraft) reports the current condition of the aircraft systems and operation to the pilot in the air. For any less than normal conditions the pilot is alerted via the Integrated Caution and Warnings (ICAW). The more severe the condition the higher alert level its awarded.
If it’s a high one, you’ll get it immediately. Other lower level alerts these will be reported based on severity level. As the pilot gets closer to base, and is in the return-to-base mode, the system will datalink all system reported discrepancies and health status to the maintenance management system.
You want to report everything to the maintenance crew. The plane is going to do the same thing. It’s going to report back to us, and in the end — we’re not there quite yet — we will know it on the ground via data link before you ever get to the ground.
And we’ll know that we’ve got, as an example, a hydraulic leak. We won’t know what part of the system is leaking in the hydraulics yet, but we’ll know the pilot’s coming back with a caution or a fault that says that the hydraulic system is not fully serviced.
SLD: There is a cultural dimension to the maintenance aspect. You bring in new aircraft that is in a very, very different CONOPS. It has very different CONOPS for the maintenance, and if the managers try to reduce it to what a 4th generation maintenance regime looks like or a legacy regime, going to lose the advantage of what really this aircraft is about.
Paramore: You’re absolutely right. And it’s one of the things that, from a [NAS Patuxent River] perspective, a double handful of us here have been approaching it with an end game perspective, even for SDD.
We always keep asking how we’re going to do it in endgame, because while we may be SDD, we know that we feed downstream. We’re feeding the guys, the maturity of different programs and different applications inside a sea of different modules.
One of these is what you were talking about is, AFRS, the Aircraft Fault Recording System. This AFRS comes with a solution set as well as what we call the HRC, which is our “fault.” If you’re an F-16 pilot or F-15 pilot, that was your MFL or your PFL, you’re Pilot Fault List or your Maintenance Fault List item.
So we have an HRC, which is a Health Reporting Code for a system. And, for example, if an actuator sends out its HRC code and says, “I have this problem,” then when we pull that into the CMMS system, when the AFRS solution sets are built, that’s kind of like your old troubleshooting tree you were talking about. It’s all electronic.
The system will say you have a HRC. And the system will suggest you start with this AFRS solution set No. 1. And you go through the tree to troubleshoot it. It will then ask you, “did this fix your problem?” And if you click on “no,” then it says, okay; let’s try this solution set. And you go down through it, and if it says, did this fix your problem; you go “yes.”
Now you’ve done two things. You’ve not only gone through a troubleshooting tree electronically that you otherwise had to do with paper in the past, you’ve also started to solidify the data in the system because you told the system via feedback. Yes, this fixed my problem.
So when that HRC pops up again, as it starts to build up these number of recurrences to say this fixed my problem, then it’s going to bypass option No. 1 and go straight to No. 2 as your solution set.
So it’s going to almost be smart thinking for solution recognition for parts that go bad, based on the HRC code.
SLD: There is a significant advantage as well to having software driven regime such as describing. Namely, significant savings of training time as you do shifts in maintenance protocols, which are not embedded in the software itself.
Paramore: Yes, absolutely. Being an avionics maintainer for many years, I know that every time we used to roll software, it required additional study to find out the capabilities of the software and what it gave us for troubleshooting. Because if you didn’t know the capabilities that were added, for example fire control radar, then you wouldn’t be able to troubleshoot when the pilot came back and said, I did this and I got this, and that wasn’t what I expected.
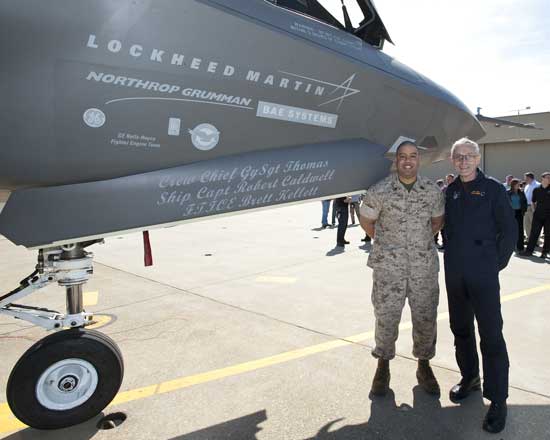
On this airplane, you won’t have that because when the software rolls, you’ll run the I-BIT. The I-BIT will tell you if the system is working the way the software is designed to work. So there won’t be a lot of this troubleshooting like we had to do like that. It will come down to, I need to replace this component or I don’t need to replace it.
SLD: Again this is a significant cultural revolution, which requires adapting organizations to what the technological advances can enable for a new maintenance paradigm.
Paramore: It is analogous to the shift of going from Windows to Macs. And if you fail to open your mind, you’ll fail the transition. Because, you know, everybody is used to their little PC running Windows, doing it the way they’ve always done it, the way they always want to do it.
It is more like Apple than Windows. Windows shifts through a series of new systems, XP to Vista to Windows 7. Now we’re in an Apple-like world, where you can run 64-bit apps in a true 64 environment and screaming past everybody else.
SLD: Could you describe the software upgrade process, which you are using in the logs approach?
(Click to read about how revolutionary such an upgrade approach is in the evolution of military aviation.)
Paramore: Lockheed has been using modular software design for awhile. And the benefit of modular software design is the ability to get more out of the applications run by the operating system, without having to update the entire operating system.
Why would you buy six different applications for your home computer and not run the updates for them? Or, why would you download several apps from the app store and not run the updates on them when it says you’ve got ten updates to perform?
So, why would you run update requests for the entire operating system when only two apps needed updates?
SLD: So the great modernization of the F-35 is somebody at a console doing code and changing something and then airplane can actually move into its next generation, its next type model series, and you can mobilize or modernize that airplane by just playing with the software.
Paramore: Absolutely. So you don’t have to build a new airplane.
And, you know, when you have different subsystems on the aircraft, they don’t all have to be updated. For lack of a better way of putting it, the communications between the two modules have to be changed. The communication architecture or, basically, the language of the two modules has to communicate in the same output language.
But as far as the core software running inside a subsystem, the software could be updated independently as long as the other system knows what to expect as an output from that system or knows what to input into that system. That’s the only other change that would need to be made.