The Impact of A New Upgrading and Sustainment Approach
An Interview with Scott Ogden
08/01/2011 – A key element in understanding the Cultural Revolution associated with the 5th generation aircraft is the dramatic change in how maintenance and sustainment can be done fleet wide and in terms of global sustainment. The F-35 will be first aircraft which enables global sustainment across the entire deployed fleet, US and allied.
Savings are not limited to cost efficiencies on a fleet-wide basis. By having much more accuracy and transparency in the parts chain and an ability to tap parts locally from various F-35 partners, the demand on the Air Mobility System can be reduced significantly.
In a discussion with Scott Ogden, retired USAF maintainer, now with Lockheed Martin, the shift from legacy aircraft to the F-35 was discussed in terms of the shift from the F-16 to the F-35A.
Scott Ogden was a maintenance officer in the US Air Force for 27 years. He worked on A-10s, F-4s, F-5s, F-16s, F-117s, F-15s, and F-111s. He has been with Lockheed for 15 years and has worked on the F-117 TSPR contract and the F-22 FASTeR contract. He has been working on the F-35 maintenance system for the last two years.
SLD: Could you explain the difference between upgrades on an F-16 and on an F-35 for avionics and related hardware?
Ogden: Whenever you’re going to change a piece of hardware, that’s what they call an “Engineering Change Proposal, an ECP. An ECP requires you to develop and/or procure this new piece of hardware, develop the integration of the software to make the hardware work, flight test the new capability, and then buy the materials and schedule the upgradefleet retrofit. Then and only then can you put it into a Falcon.
This is a three- or a four-year process to get the upgrade into that specific configuration and total numbers of aircraft you wish to effect, so you’re looking at a timeline to me that is probably four to five years to field that capability and another three or four years to get it completed in the fleet. You’re looking at a timeline of six to eight years as a conservative estimate to get a new upgrade on capability into an airplane.
SLD: And what about the applicability of the upgrade across the fleet of international F-16s?
Ogden: What I described only applies to an Air Force generated upgrade for the F-16, and it may well not be applicable across the international fleet. Whether it’s available to all 30 plus variance of F16s is an open question.
SLD: But the point being is that if you spend X amount of dollars, let’s say you spend $500,000 for this upgrade or 1.2 million, whatever it is, it’s being generated by specific budgets specific to a service.
Ogden: Absolutely. Very seldom is there an F-16 fleet-wide capability upgrade. If there’s a fleet-wide upgrade, it’s usually because of a common air frame issue or safety considerations.

SLD: This also has yielded a process whereby although the F-16 is probably analogous to the A-320 in terms of numbers of sales, the F-16 has many variants over time. So if I’m taking the Air Force, US Air Force has done a particular upgrade, pay for a particular upgrade, and now the Israelis want it, there’s no guarantee that that upgrade can be just snapped into this Israeli F-16. You’re going to have to do an evaluation as well to make sure that it works with the systems on that Israeli F-16. Is that correct?
Ogden: Yes. There would be some plug-and-play portion of it, but there would always be the testing to ensure that the other integration of the uniqueness of their configuration would plug-and-play also.
SLD: Notionally you’ve described a baseline upgrade. If we continue down this path, let us assume that I’m taking US Air Force capability that we’ve agreed with Israelis would be great to have an Israeli F16-I. Notionally, and obvious it’s dependent on what we’re actually upgrading, but notionally what kind of cost and process would this take? Would this be months to do and a significant cost?
Ogden: I’d say 18 to 24 months to get another variant. Unless they’re in a parallel path, but if you’re just looking at their critical path, I would say 18 to 24 months before they can advise what test they need, what risk reduction they would understand and especially with Israel, it would be an independent action of their own. We wouldn’t be involved in it.
SLD: You’re talking about from a generic point of view of the upgrade process that a significant amount of time, engineering skill, and cost to get a single path upgrade.
And then that single path upgrade is not available fleet-wide and then it could be available to the partners, but in the European case because you have a consortium, it could be upgraded for the consortium so that you get at least some cost savings from that, but it still requires time and extra cost for this upgrade path and so you essentially or still end up with several types of fleets.
And presumably from a maintenance point of view, if you’re deploying say three or four countries’ F-16s on an Italian air base, to state an example, there’s no guarantee just that you’re going to have commonality across those F-16s to manage the upgrade process because each aircraft is significantly different.
You may have 50/60/70/80% commonality, but there’s no guarantee from a maintainers’ perspective that he’s got commonality with that Italian F-16 or Dutch F-16 or whatever it is. They’ll have to discover it working together with those maintainers, so it’ll be craft-driven rather than system-driven.
Ogden: We wouldn’t even think of doing that. On the flight line, we would just be so segregated from the Israelis, the Dutch, or anybody else. I’d have my own parts. I’d have my own equipment. I’d have my own mission planning. I would do all of that independent of whatever other F-16s I was deployed with.
If I needed a wheel or a tire, I might share. But if it’s a part on an aircraft and it’s not a consumable, I would go back through my supply chain and get that part for my configuration. If I’m deployed, I’m not going to take the chance of borrowing a part that may look the same but have a different internal hardware with a different dashed part number, let alone a different software integration package.
SLD: The historical experience has been that when you collocate or co-deploy with allies, even though you have an airplane described as an F-16 and you all are flying F-16s, you’re not getting the advantages of that commonality that should be inherent in building a common aircraft simply because of the different variants of the aircraft you have and the fact that the supply chain has been fed to the nations separately. Is that correct?
Ogden: Absolutely. You have your own supply chain and even if you deploy with like units from your own country, you still take your own supply kits with you.
Now let’s say Block 50 is deployed with Block 50s, when you get there, you find out that you’re deployed with the team that may have the same aircraft, but you didn’t go in there deploying less of a footprint because you knew that there was going to be somebody there because you’re going to use your parts and they’re going to use their parts.
It’s more or less self-preservation and isolation from it. I even deployed two 117 squadrons and both squadrons took their own kits.
Airmen 1st Class Ronald Maynor (left) and Ryan Macz (right), both electrician/environmental specialist from the 455th Expeditionary Aircraft Maintenance Squadron, place the “remove before flight” reminders back on the F-16 Fighting Falcon, Dec. 10. These reminders are placed on the aircraft to remind the crew members to inspect the aircraft thoroughly. (Credit: 455th Expeditionary Air Wing 12/10/09)
SLD: This is all built around a local ownership either by base or deployed squadron, so local ownership is the rule of thumb.
Ogden: Right. All of your CONOPS and all of your traditional standard operating procedures are that you can operate as an independent unit, you’re staffed that way, and you’re manned that way.
That’s going to be the big cultural thing that will take some time for the synergies that we have and for people to understand that. Some services still today, as you have heard many times, do not want somebody else to have access to a part that they think is theirs.
SLD: This maintenance culture is based on several decades of historical experience. But this experience is dysfunctional to the strategic environment in which we find ourselves. We’re in a strategic environment where our allies and we, with probably the exception of Asians, have stringent defense budgets. So you’re going to have less aircraft. You’re going to more frequently wish to leverage one another’s capabilities.
From an operational tempo point of view, if you continue to have this kind of segregated maintenance legacy, it’s going to ensure that basically the capability of our allies and ourselves collectively goes down if we don’t find a way to take advantage of the cultural revolution inherent in common technology.
Ogden: The challenge is to have the Services accept the cultural change that will afford them the ability to harvest the economies of scale, and the common spares pool.
Let’s say it’s an upgrade to an aircraft that you want to do and your aircraft are deployed into Europe, okay, normally we would never send an aircraft into Italy and contract with Italy to do an upgrade on an F-16. Even if they could, we would not do that. We would go somewhere that it was US organization or US administered contract to do the upgrade.
Let’s say you land at a an F-16 base in Italy, you got to go back through your base supply to get a part shipped in to you with your crew to come out and take care of that airplane. Now the airplane sits on the ground until you get maintainers out there to take care of the airplane.
In the US Air Force process until an airplane is on your base for seven days, it still belongs to the unit that flew in the airplane. So if I’m flying cross-country, the unit, even if it is another F-16 base, they may help me, but they aren’t responsible for repairing that airplane till after seven days because that’s just the process that they do.
They’re going to say, “Okay, we’ll help you with the part. We’ll do this. We’ll give you a mechanic,” but most of the time you end up you take care of the airplane across country.
With the F-35A and the ALIS system, when the airplane drops in, we know what part, kit is available from what nearest base, we know a worldwide warehouse we would ship a part to a location to that tail number for that person to put that part on the aircraft and fix it.
This is because we have no contract limitations. We know that we’re responsible for aircraft availability and if an aircrafts down, we know and see that immediately with ALIS and we make the determination to send the part right there.
It is not a matter of the base having to decide the prioritization going back to their own, working through their base supply. And if it’s an Italian F-35 that lands a UK base, from a technological point of view it does not have to make a difference. The part would go right into the UK and be shipped to that tail number.
SLD: With the F-35A, the USAF is provided with a common configuration, a common aircraft. How does that reality potentially change the maintainers’ mental furniture and affect operational rhythms?
Ogden: What happens off the flight line would really be invisible to the user. The war fighter would not see anything different. He would just know that the parts are there faster, it’s the right part, it will integrate with his aircraft and he doesn’t know where it comes from.
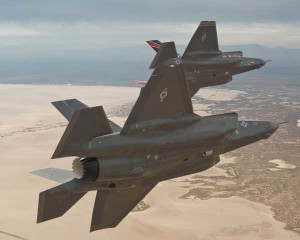
What does change is the turmoil the war fighter does not see. It changes the business application. It changes the priority of parts. It changes the way the OEMs refill the consumed part and forecast the repair of the part that just came off the airplane. All of these things are happening in parallel and subsequently much faster.
Now what it does do differently is on an F-16, an avionics’ problem would require maybe three specialists would have to troubleshoot the aircraft to say, “Here’s how many people I need to deploy to fix this airplane.” With the F-35, you get a multi solution that tells you what part will meet you at the aircraft and you don’t necessarily need a technician, three of them to go troubleshoot the airplane. It’s already done.
So the tempo for the flight line guy, for the war fighter would be: I have better prognostics, more accurate indication of what’s going to happen. And when I get there, the part will be there. I don’t have to wait for it to be issued from supply, take the part with me, and then try and move it commercially or move it through Air Mobility or whatever, drive it to the other base.
The F-16 becomes a logistics’ challenge from a war fighter perspective when it cannot fly; I need to get technicians there. The pilots probably going to come home until I get the aircraft fixed or he might stay with it. I’m talking to a maintenance guy at another base to see if he’s got the right equipment that I can even hook up my power and generator and everything else to troubleshoot the aircraft. In addition, I will need equipment for flight line testing.
With the F-35A, the ability to diagnose and test are built into the plane and provides the problem identification information up front. You can determine what you need without deploying a slew of technicians just to find out what you need to do.
SLD: Could you give us an example of the impact of the shift from the old to the new?
Ogden: OK. I will lay out a baseline code three scenario. Code Three is when the plane is broken and can’t fly again until it is fixed.
I’ll lay out the timeline and describe the numbers of people that are involved in that process of fixing and turning that aircraft, then we’ll lay down a code three timeline as we see it for an F-35 with the numbers of people involved in getting the plane flying again. I’ll be conservative in the code three numbers that I would send out is that we’re going to fix it the first time we look at it.
For the sake of this example, let us assume that you have a flight control problem. It could be that it is a hydraulic problem or an electrical problem. When the pilot lands, he says “I’m code three for flight controls,” which he has to do at that point in time is he goes through debrief. At the same time that he’s going through debrief with whoever’s in there, whether it’s a pro super or a crew chief, usually it’s going to be a pro super or an expeditor, somebody that’s going to go listen to him and then the crew chiefs going to get ready to refuel or get ready with the equipment.
We’re going to deploy the equipment out there with probably a flight control specialist and hydraulics’ guy to make sure that we know what’s going on along with the crew chief. They’re going to run the system to see if they can duplicate the flight control problem on the ground. At that point in time, they’ll make a determination that it’s either hydraulic or it is electronic or an avionics’ problem.
Then they’ll order the part and/or do another check to make sure they’ve isolated it correctly. At that point in time usually the pro super or the expeditor gets involved and they go and make sure that the right order of the part, go to supply and give him the permission to order the part and then begin to bring the equipment in and the technicians to actually do the repair may or may not be the same guy that troubleshot the aircraft.
At that point in time, they’ll do the repair of the aircraft and they’ll either run the aircraft or hook up hydraulics and/or electrical power to the aircraft to see that they’ve fixed the aircraft. That typically takes I would say two to two and a half hours, maybe even three hours to get to the point where you know what the problem is and you’ve made the determination that you’re going to order this part or fix this avionics’ part.
For the F-35, the diagnostics are done even before he even lands; I know whether it is an electrical problem or a hydraulic problem. So right there I am saving two to two and half hours of several people’s time.
The assessment phase is done automatically through the PHM (Prognostics Health Management). Now when that occurs, at the same time, ALIS has already go into the supply chain and told you whether or not you have the part, so you don’t have to wait. The part may even be issued to you before the airplane gets in the chocks.
When the pilot lands, there’s no need for him to really debrief, you’ve got default isolation, you’ve got it loaded into your PMA or your laptop, now you could in-turn when he goes in to debrief and does the physical debrief, you’re already out there fixing the airplane. If it’s a card, if it’s a hydraulic component, it’s going to take you more time. You’re going to do some physical work.
But the fixed phase is already begun while the pilot and you are going into debrief. You’ve already got someone out there.
SLD: So you’re saving time on the assessment phase and secondly you’re saving time in terms of the machine is scanning the database to determine availability of the part. The machine has the role of automating the knowledge of what’s wrong and also has an ability to scan into the system to determine parts availability, so I save manpower simply by delegating this capability to the machine.
Ogden: Now remember, on the F-16, I had to deploy test equipment and our support equipment to go run the airplane to validate the equipment. I have to have a supporting cast that I’ve got running behind the background here too.
Before I can even order the part, I don’t know what’s wrong the aircraft so I have got a supporting cast of flight line guys making decisions on how to prioritize the equipment that’s on the flight line. On a F35, my test is usually the aircraft. I don’t need several unique pieces test equipment. It has already told me when it hits the ground what is the problem.
SLD: So another cost savings is the equipment is built into the aircraft rather than a whole different team to maintain, move about, repair, test equipment external to the aircraft.
Ogden: Plus, when I send out my initial guys, they’ve got to go to the tool crib and get paper tech orders to go troubleshoot the aircraft of which they don’t know what the problem is yet. While I’ve got the hydraulic guy, the avionics’ guy, and maybe the electrician all in there getting their tech orders to go out and troubleshoot the aircraft. Guess what, the PMA already has told me it’s this particular card or it’s this component and the probability of that component is where we are focusing our dollars to make sure that we’re making quick and accurate decisions.
This means now I don’t need all these folks. I don’t need to stand in a cue. I don’t have all the wait times for people to either have eliminated the problem or decide it was a problem and then go back into the supply chain and see if I have it, have these folks stand down while we’re waiting on the part.
As a flight line maintenance guy, I love it that I’m going to be able to tell the aircraft when it lands whether I can turn it next time, prioritize the right kind of people to get over there and fix the aircraft with the parts and their tech orders are already with them.
It’s electronic. All this digital backbone becomes a very big leverage to the sustainment guy on the flight line. It’s our processes that we’re going to have a difficult time changing.
Let’s just say I shorten the queue time 35/40%, which is easy in my mind to achieve. This has a significant impact on how I manage my maintenance process.
Currently, we have four-hour, eight-hour, and 12-hour turns, right, or fixed rates. We’re going to measure that in half hours and hours and two hours, not the typical four/six/eight/12 fixed rates with the new systems.
The guy on the line can say to the ops commander: Hey look, I fixed 25% of my aircraft at landing a code three, I can finish the fix in less two hours. That means if I typically I’m having 40% of my aircraft are landing code three and 10% of those I can fix in two hours, and that’s how you build your schedule from how many airplanes do I commit to make the first go: What number of spares do I need for a second go? And if there is a third go, what’s that descending number of aircraft I should plan on flying? A 12 turn ten, turn eight or how do you want to do that?
With the F-35, I’m predicting that you’re going to be able to come up with a much more predictable flight rhythm. I will know I’m going to fly and how I’m going to fly that.
SLD: Reducing the numbers of parts needed, and providing an ability to use parts locally will lead to significant reductions in demand on the Air Mobility System to support forward deployed operations. A shift in how the combat air force is supported will in turn lead to significant savings or shift in demand for the Air Mobility System which of course includes both tankers and lifters.
I think there’s a very significant savings to be had in having a more transparent and fungible supply chain where I could have at least intellectual possibility if I’m in Italy having the Italians give me the parts.
Ogden: There is an avalanche of savings to be had from a new maintenance regime and approach enabled by the technology of the F-35A for the USAF. What you’re just describing here is just that. How does the new maintenance capabilities, in turn, offer you more savings because you’re reducing air lift, volume, weight, cubes, warehouse space. Sometimes in the US Air Force, we fly parts right past each other going from one unit to the next when it could’ve been much more efficiently managed through a worldwide distribution. I think you’ve hit on a very big point.