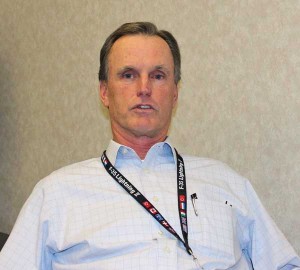
01/30/2012 – During Second Line of Defense’s annual visit to the F-35 manufacturing facility, Frank Dougherty, Vice President, F-35 Production Operations provided an update on F-35 manufacturability. Dougherty has extensive experience with both the F-22 and the F-16, and has significant domain competence in what it takes to build a combat aircraft.
SLD: We went to the factory where it was clear the focus was on ramping or making sure that you would be producing four aircraft a month. That, that’s the target goal under the current funding and planning.
Dougherty: Correct.
SLD: And basically, by July you are putting out Air Force 20, which would be the first plane in the four per month cycle?
Dougherty: Right.
SLD: How are you going about organizing the four per month, and what is the status to get to the four per month?
Dougherty: AF20 is actually about half way through final assembly at this stage. Production along the line is adjusting as we ramp up to the four per month. The various parts of production are positing themselves for where they need to be to support the four per month delivery starting July of next year.
And then after that we actually drop back down to two per month for the next couple of months.
SLD: Could you explain the concept of a software upgradeable aircraft and how this affects production?
Dougherty: Obviously, you’ve got the aircraft structure of the aircraft, but then the electronics will be upgradeable throughout the full life cycle of the aircraft. From a manufacturing perspective, the physical elements that give you the stealth of the aircraft will be good for the life of the aircraft.
The electronic upgradable portions of the aircraft, and the way it was designed to be able to be upgradable over time to your very point either through minor hardware changes that are just basically cards which can be slipped in and out, and then downloading a new program. So we’re already forecasting over time the software upgrades that will provide enhanced capabilities ongoing through the life cycle of the aircraft.
SLD: What has been the impact of the Japanese buy on the esprit de corps on the assembly line?
Dougherty: Last week with the announcement of the Japanese buy, that was a big impact for us because I think everybody recognizes that Japanese as a pretty sophisticated customer. And if they’ve done an analysis of understanding where we are, and what this aircraft’s capable of, and how actually mature it is at this stage of the game and to be able to commit to that buy, it gives confidence to the other potential customers out there.
But it also gives confidence to our workforce that the work we’re doing has been recognized by folks out there who really know how to evaluate what this kind of aircraft can do.
SLD: How can workflow be managed to surge production?
Dougherty: Actually, at this stage of the game, we’re probably too late to stay at four, but we have the capability, and we have the capacity, and we can flex back up as quickly as they would make a decision to allow us to do that.
But we’ve actually, at the very beginning of line, we’ve actually dropped back down to two per month already, and loading the front of the line because that’s what the current quantity demands currently.
But we’ve laid out the factory to be at the ultimate footprint that we’re going to operate at. So we’ve got the capacity, and the footprint for the stations, and we’ve made our line flexible enough that we can both add positions with the tooling for the number positions, for the number of aircraft we’re going to build a month, and also adjust for the mixture of the variance that we will build.
Obviously, with the three different variants going down the line, they have unique characteristics. But we’ve made the line flexible enough, so just by loading a different hard tooling into the line that we’ve got out there; we can build at whatever variation that they want.
And then also whatever actual physical rate that we need to deliver at, and ten, at the next stage, fits very nice in the format we’ve got laid out here because of the stations we’ve got, and the position we are to your point lead time away, order the hard tooling that we need, and then just load the line in the configuration, and the sequence that they want to buy the aircraft.
SLD: Steady demand at 10-20 per month will certainly lead to increased efficiencies and lower costs per unit.
Dougherty: It does. If we’re out here building two per month, a worker out there has got to do ten days worth of work before they go repeat the work that they’ve done. They work in a station, and they perform an amount of work every ten manufacturing days. There’s 20 manufacturing days in a month, so they will do ten days worth of work before they repeat that, and they’ll repeat that ten days worth of work twice in a month.
If we get to go to ten a month, they’ll do two days worth work before they go repeat what they’ll do in that station, and they’ll do that ten times a month. Imagine how much more efficient they can be doing a smaller scope of work repeated much more often, consistently in that station.
And if you have a new variant move in there, we’ve built the tools so they load very similar, little bit different materials, and little bit different in terms of the size and sequencing of the wings and such.
But that work is easily remembered if I’ve just done it two days or four days ago, whereas if I had to do ten days worth of work, and then do a different variant with little bit different sequencing of that, you know I’ve got to refer to my work instructions more, I got to refer to my engineering more. It takes more time.
SLD: Another aspect of the production approach which is not widely understood outside the program is what the SDD phase really was all about for the manufacturing phases. Manufacturing technologies and approaches have been a central focus in SDD and in a certain sense much of the advanced manufacturing capability has already been paid for; And this radically different than the legacy aircraft manufacturing approach.
Dougherty: When we built the SDD aircraft, we did it in the production tooling, and the production methods. That way we’d use as we went forth into the actual low-rate production phase of the program. And so we’re just growing right out of that build into the what we’re calling production phase of the program, but continuing to mature the same process, the same tooling, the same methods that we would use during the SDD phase.
SLD: There is as well a significant misunderstanding outside of the program of the very different approach to designing, testing and building the F-35 versus earlier aircraft. This program was set up is radically different from the beginning to essentially have a surge production capacity. Is that a fair statement of kind of a disconnect from a certain template of understanding what this is all about? It’s a very different template than a Legacy Aircraft.
Doughterty: I think with the way entering development tools have developed over the years, we’ve gone from having to do hard mock-ups, hard tooling, put together a aircraft. Stretch out actually mock-up harnesses, and then develop which way you’re going to build those, and build physical prototype models that came through.
Now with the new electronic way you design an aircraft in a scope, and proven out over F-22 and moving into F-35, all of that hard mock-up, and hard physical build up that you had to do just to verify links, and runs of all the different tubes and harnesses, and such that go through the aircraft, has been eliminated that you can essentially design that in electronically, and the very first units you build, you build the way you build the production aircraft.
You actually design it, and route it, and everything else electronically, so when we translate that to installing it in an aircraft, we’re doing it on the very first model is the way we’ll do it in production.
SLD: The digital thread production model?
Dougherty: Yes.
SLD: And also not widely understood is how so much of this approach has come from innovation in the commercial aerospace sector. Builders of the 787 and A350 certainly have pioneered a lot of this. And even the 330 tankers are an example. To develop the tanker, Airbus had to redo the entire 330 as a digital aircraft in order to actually come up with an effective name of building a tanker. And that’s kind of a footnote to how wider the difference is from when the A330 was originally designed 30 years ago.
Dougherty: I think so. And in fact, I was responsible for building F 22s, prior to coming here. And of course, that was the first Fifth Gen Fighter, but it was really designed around performance, not around manufacturability.
But we learned a lot from that period, and learned a lot from what we do on F 22, and were able to design in, into that digital thread, design in manufacturability, and be able to set up tooling, and methods and sequences.
From the very beginning, we knew how the aircraft would go together. We knew where the issues would be, and we were able to proof that out on the very first SDD Jets. So as we transformed into delivery production, we were ready to build a aircraft the way it needed to be, and that’s very different from the experience I had back in the old days when I built F-16s in the line out here, and at even the very beginning of the F-22.
We had some dramatic changes we had to make early in that because we were really just learning how to use those digital tools to translate those, but we’ve taken all those lessons learned now, incorporated them into our design, and built an F-35, and had dramatically different results right out of the chute.
SLD: How important is manufacturability for risk of being successful global program export, and ability to build a global fleet aircraft?
Dougherty: It’s really the key to affordability. From the very beginning, it was designed with the intent that we would be able to build one a day, and deliver one a day. And so it was designed, so it would go together, so it would be compartmentalized, so the work could be broken down into those segments, and so the aircraft could progress through, and quickly come together, and when it came off the end there wasn’t a lot of tweaks, and adjustment changes to make.
The aircraft was ready to go put gas in it, load software in it, and fly it, and that is different from with the more handcrafted F-22s that we knew we weren’t going to build, but a few hundreds of those. That was really designed for performance, and optimized for the performance of the aircraft after it was delivered. This one obviously has the performance characteristics in there, but we were really leaned towards the manufacturability, and affordability available to put out one a day.
Featured Image: F-35B arriving at Eglin AFB January 2012 Credit: 33rd Fighter Wing
Accompanying Videos From the Interview
In this video, Frank Dougherty discusses the key differences between making the F-35 and modern commercial aircraft and legacy aircraft, whether military or commercial.
In this video, Frank Dougherty discusses a key point about the F-35 compared to the F-22 being that is both a high performance aircraft as well as designed to produced in quantity. Manufacturability is central to the impact of the F-35 on global fleets.
What much of the F-35 debate misses is that the System Development and Demonstration Phase of the Program front-loaded a significant manufacturing capability. The US taxpayer and foreign partners have already paid for the F-35 manufacturing capability, which will be leveraged in a surge production.
In this video Franck Doughtery, Vice President for F-35 Production Operations, explains to Second Line of Defense what the impact of SDD is upon production in 2012.
The F-35 is currently being produced at 4 per month; with the anticipated budget this will be reduced to 2 per month; the line can move to 10 a month in a few months of lead time. The plane is designed to be mass-produced, and with foreign orders coming in surge is a clear option. Frank Dougherty, Vice President for F-35 Production Operations explains in this video to Second Line of Defense the approach.
The F-35 is a unique aircraft as Ed Timperlake explained earlier the plane is in constant evolution as the software is upgraded. But with the F-35 this does not drive hardware upgrades, but is shape by the chip and integration structure ABOARD the aircraft. In this video, Frank Dougherty of Lockheed Martin, the VP in charge of F-35 Production Operations, explains how this works.
The global nature of the F-35 program is crucial to its viability and impact on 21st century combat operations. Here Frank Dougherty, Vice President of F-35 Production Operations, talks to Second Line of Defense about the impact of the foreign partners seen from Fort Worth.