2013-03-07 By Richard A. McCormack, ed****@***************ws.com
http://www.manufacturingnews.com
Structural changes in U.S. industry over the past 30 years caused primarily by the financial sector’s insatiable quest for profits have left “gaping holes” in the American system of scaling up new technologies to large-scale production, according to preliminary findings from a study conducted by 20 professors and their students at MIT.
“The fact is that resources that used to be there as public goods — things that companies could draw upon if they did not create those resources themselves — have dried up and shrunk and moved away,” says Suzanne Berger, MIT professor of political science and co-director of MIT’s Production in the Innovation Economy (PIE) project. “No company, not even the largest U.S. multinational, can create in-house all of the resources it needs to scale products up, and this is all the more true of startups and main-street manufacturers.”
In a “fact-based” study of 255 companies in the United States, Europe and China, the MIT professors found that the United States has — for the most part — lost the ability to transition a new product or product innovation to commercial production. The problem not only persists among America’s best manufacturers, but is even more pronounced among venture-capital backed firms trying to commercialize innovative ideas.
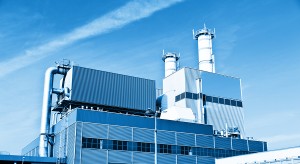
Unlike their competitors in Germany and China, American manufacturers and innovators are “home alone” when it comes to scaling up a product or innovation to commercial production, says Berger. Adds the Production in the Innovation Economy’s interim report: “Its not just that factories stand empty and crumbling: It’s that critical strengths and capabilities have disappeared that once served to bring new enterprises to life.”
In its two-year study, MIT decided to look from the bottom up on the system of new product commercialization and production. They talked with company executives about how they trained workers, found capital, invested in equipment and identified suppliers needed to manufacture a new product. The question MIT intended to answer was this: “We know the United States is strong in innovation, but can it bring these innovations to market?”
Among its conclusions:
- “There are many serious reasons to worry about the fate of manufacturing in the United States.”
- “Financing, capabilities, and customers and suppliers pull technology development abroad.”
- “The most urgent challenge for U.S. innovation and production is to rebuild the capabilities in the industrial ecosystem.”
The MIT cross-disciplinary team studied a group of 150 startup companies developing physical products that spun out of MIT laboratories from 1997 to 2008. They visited growing manufacturing companies in Ohio, Massachusetts, Arizona and Georgia. And they conducted interviews at 30 large U.S. multinationals. They compared them to 32 similar companies in Germany, 36 in China and 10 from other countries.
In looking at the largest firms, MIT found that the American industrial landscape has changed dramatically due to a financial system that forced them to focus on core competencies.
“Globalization and low-cost imports from China have made a difference, but we believe the real change took place in the 1980s when you began to see scaling down and changes in financial markets that made it very desirable to move your production capabilities out of your own four walls and become an asset-light company,” says Berger.
This trend “has left gaping holes in the industrial ecosystem that have started to have a huge impact” on the American economy, says Berger. “A lot of good came from those changes: the fact that you can access production capabilities that you don’t have to create in-house, even if they are overseas. That should allow innovation to come to market more rapidly and in some cases it has, but we did not have the accompanying public policy changes that would have allowed much of our manufacturing economy to have benefited from these changes.”
The danger now, says the MIT study, “is that as U.S. companies shift the commercialization of their technologies abroad, their capacity for initiating future rounds of innovation will be progressively enfeebled. . . Looking even further down the food chain beneath the companies to the laboratories that can generate innovations in the first place, looking at the university laboratories that are the terrain we know best, we saw reasons to fear that the loss of companies that can make things will end up in the loss of research that can invent them.”
The companies that spun out of MIT laboratories did well through their first 10 years, securing additional rounds of funding from venture capitalists. It was only at the point when they were ready to move to commercial scale that they couldn’t find the resources to scale up production, says Berger. “That is when you see foreign governments moving in and you begin to see these companies being bought up by strategic partners.”
The point at which a company would start generating the biggest payoff with growing revenues and profits — after investing in plant and equipment and trained workers — is not happening in the United States.
The same was true of the fastest growing small and medium-sized manufacturing companies in the United States.
“When we compared the main street manufacturers to what we were seeing in Germany, we realized that even though these were very innovation firms, they just weren’t growing fast enough,” says Berger. “The level of growth of their profits, the speed in which they could bring a product to market, the increase in the jobs that they could create seemed to be sub-optimal and we came to realize that the problem is that they have to depend entirely on their own internal resources. They are ‘home alone.’ ”
In Germany, MIT found not only “legacy resources, but also access to a rich and diverse set of complementary capabilities in the industrial ecosystem,” says the interim report: “suppliers, trade associations, industrial collective research consortia, industrial research centers, Fraunhofer Institutes, university-industry collaboratives, technical advisory committees.” While Germany has almost 300 different organizations involved in these types of programs, there are “thin and shrinking resources available to U.S. manufacturers across much of the country.”
In China, MIT professors found firms “that excel in scale-up to mass manufacturing not because of low-cost labor, but because of their ability to move complex advanced product designs into production and commercialization.” American firms are drawn to these companies because of their “specific capabilities in knowledge-intensive scale up [that] involve reverse engineering and re-engineering a mature product to make it more rapidly and efficiently; making designs into new-to-the-world products and processes; and indigenous product innovation. In each of these categories, PIE researchers interviewed Western companies and their Chinese partners and walked through the Chinese plants with engineers to track how exactly innovation was being produced.”
It is now imperative for the United States to create a similar industrial ecosystem that includes organizations involved in risk reduction, risk sharing, risk pooling, “bridging” activities and training, according to MIT.
Examples include the recently created National Additive Manufacturing Innovation Institute in Youngstown, Ohio, and the 17 other similar institutes that have been proposed by President Obama in the $1-billion National Network for Manufacturing Innovation; a strengthening and expansion of private-sector organizations like Sematech; and industrial R&D consortia tied to work being done at national laboratories and universities, similar to what Timken Co. has done with the shifting of its materials coating R&D laboratory to the University of Akron.
“The key point is the creation of resources that many diverse players can use and have access to,” says Berger. This is a far better utilization of resources than direct grants to companies for commercialization activities, or tax credits or tax write-offs to individual companies given by state economic development offices. “When those companies move away, which may be entirely rational, there is nothing left in the community,” says Berger. “Whereas, if you are creating an institution that multiple actors want to participate in, even if one of them goes away, there is something left that has attractive power. We would really like to see the creation of these institutions that have these coordinating, convening, risk reduction capabilities from multiple actors — universities, private companies, for workers and training — rather than the distribution of benefits to individual companies.”
Creating such an infrastructure will cost money, but is essential if the United States wants to get back into the global economic competition. Funding should not come out of the hide of existing R&D accounts because then “you are eating your seed corn and that is not a good idea,” says Berger. “We need to continue feeding that since we are not seeing that kind of activity taking place any more within big companies, which are buying the startups or licensing the technologies. [Corporate] R&D is completely non existent at this point, so if we don’t do it in the universities and public laboratories then we are really cooked,”
There are opportunities for American manufacturing companies, however.
All of the start-up firms that are being spun out of universities and laboratories need manufacturing suppliers who can make the products. “Those capabilities need to be very close by,” says Berger. “There is a lot of potential out there for American manufacturing.”
MIT is considering the creation of its own manufacturing initiative because, as the interim PIE report points out, “it is hard to figure out who will benefit and how from our research, or what our students will have as opportunities in career and life” if the country does not have the ability to produce what it invents.
MIT will produce two books from its research initiative, to be published in the fall, along with a major conference in Cambridge, Mass. It held an event at the National Academies of Sciences in Washington, D.C., in late February to discuss its initial results. The Academies’ main lecture hall was overflowing with attendees. A briefing later on Capitol Hill resulted in a similar level of interest, indicating that the time is ripe for change.
The principal investigators also briefed Obama administration chief economist Robert Rubin and his staff working on manufacturing issues, Rebecca Blank, Acting Commerce Secretary, and David Danielson, the Department of Energy’s Assistant Secretary of Energy Efficiency and Renewable Energy (and a former founder and director of the MIT Energy Club), also to favorable reviews. Patrick Gallagher, Director of NIST, and Arati Prabhakar, Director of DARPA, participated in the National Academies panel on the interim PIE report along with MIT President Rafael Reif. The challenge is gaining buy-in from Congress.
The preliminary report is located at