2013-11-01 By Robbin Laird
During my October 2013 visit to Italy, I spent two days at the Cameri F-35 facility.
While there, I had a chance to discuss the facility and the approach of the Italians with Debra Palmer, Lockheed Martin’s General Manager at the facility.
Palmer comes from a military family and herself served in the US Army. She has many years of experience in the defense business, first with General Electric and then with Lockheed Martin. Her position at Cameri is the first that she has held with Lockheed Martin Aeronautics.
We discussed the standing up of the facility, the role of Lockheed Martin in the process, and the Italian approach to the facility within a European context.
Palmer: The project is a green field project, meaning that it is a new build facility. The actual construction began on February 2011 and we were able to start our first F35 production line at the new facility in about 18 months.
The Japanese will configure their F-35 facility within existing plants for Mitsubishi Heavy Industries (MHI), but here the Italians built from the ground up.
Laird: How would you describe your job in terms of your key interfaces?
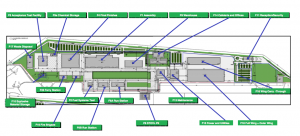
Palmer: As the LM GM at Cameri I have several key relationships within which to work.
First, LM works in a Joint Venture-like arrangement with Alenia Aermacchi (AAeM) to assist in the standup of the facility.
Second, I am the primary LM interface with the Italian MOD and play a role in representing their interests at LM and to the Joint Program Office (JPO).
And I interface with the JPO; for they are the contracting customer for all planes built in the program.
I also focus on ensuring that Italian companies are in position to have opportunities within the F-35 program, by championing their designation as a qualified supplier.
Italian companies are well positioned within the program and will be in position to receive anywhere from 8 to 12 billion dollars worth of work during the production phase of the program.
Sustainment presents a whole additional set of opportunities for Italian industry as well.
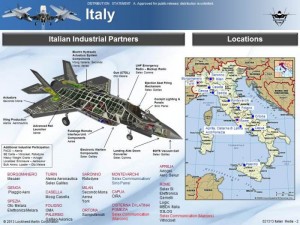
Laird: Might you describe the facility and the process of standing it up?
Palmer: There are 22 buildings with more than one million square feet of covered work area.
The plant mirrors the processes followed in Fort Worth. It is really to be viewed as an extension of the FACO and Wing production lines to provide capacity and flexibility to the F35 program.
The Italian commitment is to ensure that the planes built and maintained here would be to the same quality as if they were built in Fort Worth and for the same price; and not one penny more.
We have three types of Lockheed personnel at the plant.
The first encompasses the expats who are here to work and advise, in partnership with Alenia Aermacchi, for the standup of the entire project and system. There are over 30 expats at Cameri.
The second encompasses long-term TDY personnel and these are technicians and process specialists who are in the plant for several months at a time to train specialized tasks.
The third involves surge support from technicians from the US for generally less than a month to provide support with regard to a very specific task.
In reverse, Alenia Aermacchi has sent supervisors to Fort Worth for orientation and training in the F-35 program for up to two years at a time.
We start by recalibrating the processes within Fort Worth at Cameri but as we do so we learn from the Alenia people as well so that processes get better.
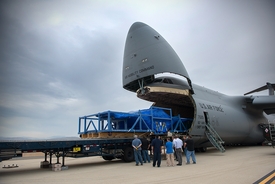
We can take that learning back to Fort Worth as well.
And many of the LM personnel who have been involved at Cameri will work with the Japanese next.
In other words, we are part of building out a world wide manufacturing process at Cameri.
Laird: The plant and facilities have been built from the outset to provide for F-35 sustainment in Europe and the Mediterranean.
Indeed, one might look at the facility as a Fleet Sustainment Center for the F-35 fleet in the region.
What is your take on this?
Palmer: The JPO has not decided on a final worldwide logistics strategy but it is obvious that Cameri provides important capabilities.
And from day one of operations it meets requirements for US forces.
US certifications are built in; we do not need to go through a long process of additional certifications and costs to meet those certifications.
Why would you want to fly your planes all the way back to the US if you are in the region and are operating within the region?
Laird: Could you go over the roles of the facility?
Palmer: There are three roles.
First, the FACO assembles Italian planes and those of Europeans who wish to have their planes assembled here.
Second, the plant will build a minimum of 835 wing sets for the global enterprise.
Third, extensive warehousing, an ATF facility for testing stealth and a paint facility support the sustainment efforts.
I should mention that for other European nations, there is an advantage of building the planes here as well due to EU requirements. Obviously, planes built here are built to EU standards, built in so to speak.
Laird: Let us go back over the last point.
In effect, by having the combination of a F35-tooled facility, an ATF (Acceptance Test Facility) and an Aircraft and Component Finishes paint facility, Cameri can function as the aviator’s “dry dock” to provide for battle damage repair within a regional context?
Palmer: That is a good way to look at it.
The Italians are committed fundamentally to partnering.
They look at the warehouses and support facilities here as locations where allies could establish secure facilities with their own data systems, which can be isolated for security purposes.
They understand the importance of sovereignty and national security but within an allied context.
Laird: Clearly, a key component of standing up such a facility is the human capital in such an enterprise.
How has Alenia Aermacchi gone about doing so?
Palmer: Human capital is crucial.
The plant is located in the industrial heartland of Italy; in addition to aeronautical companies like Alenia Aermacchi (AAeM), there are cutting-edge high performance automative manufacturing operations such as Maserati and Ferrari located nearby. A very rich environment for hiring a technical work force.
Alenia Aermacchi has built a blended workforce.
They have brought in experienced workers from other parts of AAeM as well as hiring new workers. There are several colleges specific to engineering and aerospace in the area from which to draw.
In addition, there are agreements with local high schools, which then teach students techniques applicable to airplane manufacturing.
AAeM has set up 90-day training sessions at the plant as well. LM has provided engineers and technicians at Cameri and we are training with both classroom and on the job techniques specific to F35 manufacturing.
I should note that the Italians are paying LM to provide this expertise. But it is also the case that AAeM has been building airplanes for over a 100 years, longer than LM and its heritage companies.
Their ability to produce is excellent so far. In fact, they have performed at the same level, or better on some parts, as the US-based production processes.
Laird: I went with Ed Timperlake and Secretary Wynne to Eglin last month. The sense of enthusiasm from the maintainers and pilots was clearly evident. I see the same around the Cameri campus.
Palmer: I came here because I wanted to be part of something which could form an important legacy for the future.
This plant will be supporting the F-35 program for the decades to come.
It is gratifying to be here and to be part of the process and I think the Alenia Aermacchi and Lockheed Martin personnel feel as I do.
It is an adventure to build out a 21st military aerospace process and to lay the foundations for the F-35 global enterprise.
These photos show workers at the FACO working on the first jet.
The workforce is a mix of older and younger workers, and provides a significant boost to the future of Italian aerospace and defense.
[slidepress gallery=’cameri-and-the-f-35′]
Credit Photos: Alenia Aermacchi (AAeM)