2015-02-22 The distributed aperture system or DAS is a key set of sensors on the F-35 which provides data for the fused cockpit system and the helmet display.
In an interview which we did at Pax River with a USMC test pilot in the spring of 2010, it was clear that the new system provided a significant advantage:
Lieutenant-Colonel Dehner: One of the new operational capabilities of the F-35B is its ability to sense the IR energy or the heat coming off the environment, a full 360 degrees around the aircraft.
It’s as if you are in the middle of a soccer ball : this is how I always picture it looking out through the facets.
I have these IR sensors all around me. And then the aircraft also detects more of the electromagnetic spectrum similar to a Prowler.
So, you do really have a lot more information that’s coming in or is available to be understood.
This capability shapes the classic question of how does one put information in a way that a human being can understand and act upon it?
Part of the answer is the way the information is displayed which enables the pilot to be a tactical decision-maker. Y
ou gain this God’s eye perspective of the world.
So, instead of being very mechanically-driven like we are in our current aircraft, in which I have to help move the radar around to make it do it’s thing, I can pull back and allow the systems on the aircraft to do that on it’s own.
Now, that’s only part of the answer.
The next piece is the Distributed Aperture Systems (DAS), that is sensing the IR world all around me.
You have camera eyes staring at all times around you, and how do I get that information across to a person that, obviously, can only look in one direction at any given time.
So the system’s interface, the DAS imagery, gets projected on a patch on your helmet, which is an improvement or a next a step from our current helmet.
So now, I have a window into this other world and I can look at information in the IR.
And as I turn my head I’m looking at the world surrounding me with the DAS information coming across.
SLD: So that the DAS system works closely with the helmet and it creates a new environment for the pilot to operate in.
You also were alluding to something I find interesting, which is this whole relationship between the classic tactical fighter and a specialized war battle manager, who’s on electronic warfare aircraft. In fact those specializations will be broken apart by the F-35.
Lieutenant-Colonel Dehner: Absolutely.
The classic tactical fighter was defined by the strike package where I’m going to have aircraft that will deliver weapons; I’m going to have fighters that will either clear the way or protect them while they go in.
And then I’m going to have electronic attack aircraft to provide another level of support.
In contrast the F-35, by design, will be able to do all three of those things with either the same aircraft or the same little family of aircraft.
So, you can prioritize different roles such as : the two on the front are the fighters today, the third is going to pick up electronic attack, and the fourth is going to do the strike.
But depending on how we’re configured, we can actually flex that real time.
“Hey, looks like the fight is actually more on your side. So, we can actually shift that focus of effort to the other aircraft.”
So, it just allows us an extremely flexible platform.
Now Northrop Gumman has recently supplied the 1,000 of these systems for integration on the F-35.
As the ramp rate increases on the F-35, which will see a significant number of aircraft deployed by 2018, obviously core suppliers like Northrop Grumman are also ramping up.
With Lockheed Martin owning 30% of the aircraft production, the performance of the suppliers is central to any effective ramp up.
According to a Northrop Grumman press release issued on February 18, 2015:
Northrop Grumman Corporation (recently supplied the 1,000th AN/AAQ-37 Distributed Aperture System (DAS) sensor for integration on the F-35 Lightning II aircraft.
The six infrared DAS sensors on the F-35 provide full spherical situational awareness to the pilot, day and night. The DAS provides a revolutionary capability to autonomously detect and track aircraft and missiles in every direction, while projecting video directly into the pilot’s helmet mounted display and eliminating cockpit obscurities. With DAS, the pilot has an unprecedented view and awareness of the surrounding world.
In flight testing, the DAS has demonstrated the ability to expand into additional missions and platforms, including ballistic missile defense, hostile ground fire detection and unmanned aircraft operations. DAS flight demonstrations have included tracking a rocket to over 800 miles (1300km) distance.
“With 1,000 sensors delivered, we have demonstrated the maturity and affordability of our DAS technology,” said David Partridge, director, F-35 Radar and DAS programs, Northrop Grumman. “The system provides fifth generation awareness and protection unparalleled in legacy aircraft and continues to show its versatility and applicability to a wide range of additional missions and platforms.”
As a principal member of the Lockheed Martin-led F-35 industry team, Northrop Grumman performs a significant share of the work required to develop and produce the aircraft. In addition to producing DAS, Northrop Grumman designed and produces the F-35’s AN/APG-81 radar and communications subsystems avionics; produces the center fuselage; develops mission systems and mission-planning software; leads the team’s development of pilot and maintenance training system courseware; and manages the team’s use, support and maintenance of low-observable technologies.
But it is not just in the United States where the DAS is produced.
According to this article published in Gizmondo Australia by Campbell Simpson and published on February 20, 2015:
The Lane Cove West Business Park on Sydney’s north shore is a sleepy little place, but inside one of its buildings, behind these doors, something very high-tech is being created. Rockwell Collins Australia, a subsidiary of its American parent, is hard at work building an integral part of the world-class sensor suite that goes into the F-35 Joint Strike Fighter.
The part in question is the Distributed Aperture System, an electro-optical lens-and-sensor array in a set of six that are arranged around the body of the F-35 and tied into both the flight control systems and the pilot’s ridiculously advanced helmet. The DAS is, in essence, an incredibly high-tech camera, but the arrangement of six on a JSF airframe gives the pilot a 360-degree, 3D, true-to-life live feed of the terrain and flight space around them. It also tracks and catalogues nearby planes, incoming objects and potential threats.
This is what the DAS does:
A little smaller than a soft drink can, the Distributed Aperture System requires incredibly precise optics and both optical and infrared sensors and therefore minutely accurate manufacturing by a highly trained team. The facility to build the DAS had to be custom built at Rockwell’s Australian offices, with air-leveled tables in a class 10,000 clean room and a final testing system that is the only one of its type in Australia. Rockwell wouldn’t share any info on the individual price of a DAS with us, but you can bet they don’t come cheap.
Intricately tied into the DAS and every other system is a F-35 pilot’s helmet:
The helmet includes projectors that show a heads-up display on the pilot’s visor, and when switching to DAS mode the pilot can look around and through the jet’s airframe, literally moving their head to see through the fuselage and underneath the wings. Since the F-35B has the capability for vertical landing, a system like Distributed Aperture is of huge advantage to a pilot’s situational awareness.
Here’s the clean room where the DAS is built, hidden away in Rockwell Collins’ facility and locked behind several sturdy doors:
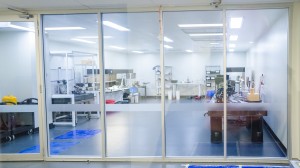
The Aussie lab is the sister of an identical one in the United States, and has been tasked with building 40 per cent of the total number of DASes required. With 180 JSFs being rolled off the production line per year during full-scale manufacturing, Rockwell’s contract to produce at least 6 DAS units for each — not counting replacements and spares — means the Australian operation will be producing 432 of the 1080 total. At the moment, only two staff work full-time in the clean room, but Rockwell wants to increase that to eight once a team with the right level of qualifications has been assembled.
Australia has orders in place for at least 72 of the F-35 Joint Strike Fighter aircraft based at RAAF Bases Williamtown and Tindal, with provision for up to 100 in total including a third squadron at Amberley. (During the building’s opening ceremony, an Air Force spokesperson casually mentioned that “we’d like a few more”, too.)
The F-35′s DAS is just one of several aerospace and defence projects that Rockwell Collins Australia has under way. But when the F-35 Joint Strike Fighter finally makes its way to the RAAF’s operational fleet, chances are it’ll have one piece stamped Made In Australia on it.
According to this press release from Rockwell Collins Australia dated April 2, 2014, their role in DAS production was announced:
Rockwell Collins has entered into a long-term agreement with Northrop Grumman Corporation (to expand manufacturing of the optical assemblies for the Electro-Optical Distributed Aperture System (DAS) on the Lockheed Martin (NYSE: LMT) F-35 aircraft.
Rockwell Collins is qualifying its facility in Melbourne, Australia, to produce these assemblies.
This is in addition to manufacturing that is already occurring at the company’s facility in Carlsbad, Calif.
“With the support and investment of the Commonwealth of Australia, we’re proud to be on the path to be manufacturing 40 percent of this vital assembly in Australia,” said Nick Gibbs, managing director of Australia, for Rockwell Collins. “Our employees are very excited to be part of the F-35 supply chain with our new state-of-the-art precision optics manufacturing capability.”
The establishment of this capability is a significant achievement for Rockwell Collins in Australia and Australian industry. The contracted activity represents a challenging manufacturing task in support of the F-35 program and positions the company’s Melbourne facility for future electro-optical production and sustainment programs.
And in a story by Brent Balinski, published in Manufacturers’s Monthly on February 23, 2015, the training approach involved with DAS production in Australia is discussed.
The factory expansion, adding a new Class 10,000 cleanroom to the Iowa-headquartered company’s Sydney manufacturing facility at Lane Cove, was celebrated last Friday.
From our perspective I think we’re bringing in the next level of technology,” Rockwell’s managing director, Nick Gibbs, told Manufacturers’ Monthly.
“We’ve invested more than a million dollars to set up that part of the capability recently,” Gibbs said at the opening.
“Financial investment as well as investment in processes and procedures and training and so on.”
The site will make a contracted minimum 40 per cent of optical assemblies to be supplied to Northrop Grumman for its ultra-high tech Distributed Aperture System…..
Six months of training in the United States were required for the operator, who returned to Sydney in December.
Rockwell could not disclose in detail exactly what’s found in the sensor assemblies further than “a lot of lenses”, but Foster could say that tolerance levels were diabolically tight for putting together what comes out of the factory.
“If anything’s out a little bit that degrades the capability significantly, and also you’ve got to remember that that’s going on an aircraft that isn’t an airliner flying in a straight line at 30,000 feet,” he told Manufacturers’ Monthly.
“Keeping all that in alignment, mission after mission after mission in very cold and very hot environments is a hard thing to do. The expanding and contracting of the metals alone with respect to the optronics skews things.
“So we have to have some very sophisticated manufacturing procedures to compensate for that and then bond it all together.”
There are currently two employed in manufacturing the assemblies, with plans to increase this to eight as production ramps up.
There are plans to also take on more staff for sustainment of the assemblies and helmets in the future.
There were other flow on benefits for local manufacturing from the JSF program, said Gibbs, an example of the kind of high-tech industry to which Australia was well suited.
“The requirements for precision engineered parts, whether it’s in medical or aerospace or IT area is continuing to grow, and I think that’s an area where Australian manufacturing can shine, where there is a real requirement for precision, for adherence to process, and not just about labour cost.”
For an overview on the F-35 global enterprise see the following:
https://www.sldinfo.com/the-f-35-allies-and-global-investments-in-21st-century-airpower/
And for interviews conducted last year in Australia with some of the Australian F-35 suppliers:
https://www.sldinfo.com/an-interview-with-the-ceo-of-quickstep-an-australian-f-35-global-supplier/
And an update on one of those suppliers:
https://www.sldinfo.com/marand-australia-celebrates-first-australian-f-35-vertical-tail-delivery/