2015-03-01 When the F-35 is discussed, subsumed in the discussion is the evolution of defense supply chains.
The F-35 is built around global supply chains, and the digital systems by which the aircraft is built is rooted in a triangular relationship among the digital systems used by suppliers, the final assembly manufacturer and the maintainers. Learning moves through this triangular system.
A key part of the global enterprise for the F-35 will be the global sustainment system.
Built in part on the model pioneered in the C-17 global sustainment appraoche – where parts are commonly owned – and partly on a 21st century digital system, the F-35 sustainment system will draw upon the innovations in DoD reforms in sustainment systems.
A key element of such reforms has been building when and where possible into the legacy process sensors, which allow an ability to track the movement of parts, and where possible building a life-cycle understanding of key parts as well.
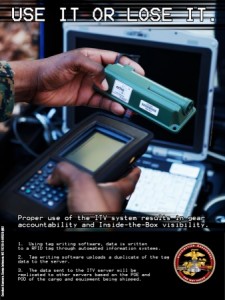
At the heart of these reforms is a simple idea articulated by Secretary Wynne when at OSD AT and L.
According to Louis Kratz:
I hate logistics!” Wynne declared and then proceeded to outline the DoD’s $180B in annual logistics expense, 32 day customer response time, lack of visibility and agility, and $70B in inventory.
Wynne accurately and simply defined the limits that the current logistics structure would place on RMA.“I hate logistics!” Wynne repeated and chided the 300 program management audience to join him.
“I hate logistics!” the PMs joined in.
Mike’s logic was impeccable as he explained:
“Whether push or pull, our current logistics are reactive. At best, unless we embrace a new paradigm, we will be still depending on the Warfighters to tell (the logisticians) what they need, then trying to supply it as fast as they can. This amounts to an industrial age vendor struggling to satisfy an information age customer. Reactive logistics-the old logistics-will never be able to keep up with warfare as we know it.”
A technological foundation for shaping a more transparent tracking system for the Department of Defense has been generated by technology, namely the introduction of unique identification and RFID systems.
In an overview on the DoD approach, Murielle Delaporte interviewed Michael Wynne and key OSD officials involved in shaping the way ahead.
UIDs have been revolutionizing U.S. logistics in the past decade both in the commercial and governmental sectors.
Nine years have past since the concept has first been introduced by Michael Wynne within DoD and in spite of multi-front resistance and obstacles, the process has now a life of its own and has passed what the latter refers to as the “tipping point”, i.e. the point of no return, as it turns out that the benefits go well beyond simple asset visibility…
As Michael Wynne stresses:
UID has become today a major underpinning on the removal and transfer of material to both the Iraqi and Afghani forces. Much like in this country, we now see Bar Codes on the side windows of automobiles for entry into garages as well as bar codes on Personal Data Assistants for payment or ticketing. This is a gratifying extension to the introduction of the same concepts in the logistics machinery of the US Government.
Going backwards, it has been challenging to introduce new sensors into older systems.
Going forward, any new platform DoD buys ought to be optimized to provide the sensor generated data, which can enhance the reliability, effectiveness, and cost savings of a management system, which in turn can shape new sustainment approaches.
The F-35 is clearly such a system.
Because the F-35 was born at a time when DOD was keenly focused on implementing Unique Item Identification (UID) and Radio Frequency Identification (RFID) technologies, the plane was built from the start with modern logistics tool sets in mind.
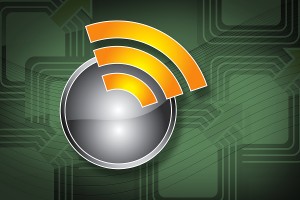
In effect, this means that the aircraft speaks a universal or global logistics language.
This common language and the digital management, which is enabled by this language, allows for the F-35 fleet to be managed globally in an historically unprecedented manner.
In discussions of new systems such as the F-35, the new sustainment capabilities built-into the aircraft through systems like UID and RFID are not really part of the public debate.
In fact, the projection of legacy approaches leads to significant distortions in projecting the future of the operations of these systems, and really leads to significant failures in understanding that leveraging 21st technologies and management approaches are part of the overall effort to shape 21st century combat effectiveness.
But how do sensor technologies translate into more effective management practices in using the data or information generated by those technologies?
How can RFID and other sensors help identify the actual workflows generated by the movement of goods and the use of those parts and goods by users in the supply chain?
How can the data or information be organized to be used at the most effective point of attack?
Or how can that data or information be organized and delivered to users in need of that information and in forms which are useable to appropriate decision making levels?
In other words, the focus has been upon the sensors tracking movement, or upon the IT system providing basic parts information (e.g., in the F-35 system the ALIS system) but how do those sensors or basic IT systems become leveraged to provide for the operational intelligence to understand the ongoing improvements in the performance of the supply chain or the de facto reform of the work flow processes?
To understand how this happens, we are preparing a series based on interviews with Globe Ranger, a Fujitsu company, based in Richardson, Texas, to provide an understanding of how one company has approached supply chain transparency, work flow management, and providing tools for providing operational supply chain intelligence to both commercial and defense customers.
Only by understanding how this is done, can the public discussion about the impact of new systems such as the F-35 be understood in terms of how the reform of maintenance systems delivers greater combat capability to the forces.
The series will begin with a series of interviews with the CEO of GlobeRanger, George Brody, who will describe the approach of the company and the software engines developed by the company to shape their logistics business.
Then the application of their approach to defense will be examined and finally some case studies of how the operational intelligence generated by the systems allow for various sectors to have delivered substantial improvements in supply chain management.
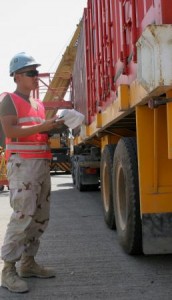
The strategic impact of such improvements cannot be underestimated in terms of cost (given the high cost of sustaining forces and weapons systems), security (in terms of knowing where weapons are located at any time), and in terms of operational tempo (providing the right supplies to the right forces at the right time).
On the GlobeRanger website, they describe themselves as follows:
GlobeRanger Corp. is an RFID software and solutions company founded in 1999 that has pioneered the creation of an information processing infrastructure at the edge of the enterprise. This enables companies to harness data that is generated outside traditional IT environments to improve their business processes and move closer to being real-time organizations.
GlobeRanger’s early product vision encompassed a range of technology components integral to the creation of an edge infrastructure. Accordingly, its iMotion ‘edge’ platform incorporated support for mobility and for data collection technologies from handheld barcode readers to RFID to sensors and beyond. This holistic vision of edge computing pre-dated the first phase of mandate driven RFID market activity.
As a result, the company can today boast of a robust and proven product uniquely designed to support edge computing across industry verticals.
The company’s mission is to provide the most reliable, scalable, and flexible enterprise edge software infrastructure and solutions at the lowest total cost of ownership (TCO).
GlobeRanger’s production-tested iMotion Edgeware platform simplifies the development, deployment, and management of RFID, mobile, and sensor-based solutions. This Edge software platform seamlessly integrates existing and new technologies such as bar code, RFID, wireless and sensor based systems preserving past investments while enabling new edge applications.
GlobeRanger’s product offerings are based on its iMotion Edgeware platform which is an acknowledged ‘best of class’ product that has consistently offered customers the fastest path to robust solutions. GlobeRanger also offers configurable applications for RFID-enabling supply chain logistics activities from manufacturing to distribution center to retail store. A nimble Solution Services team and a unit for providing infrastructure services form part of a capabilities portfolio that enables GlobeRanger to be a true single-source solution provider. Strategic partnerships with Software and Services companies have helped the company to establish a global reach and address large-scale deployments.
GlobeRanger powers some of the largest RFID production deployment in the world including the U.S. Defense Logistics Agency and Flora Holland. The iMotion platform has been the foundation for many deployments in supply chain operations, logistics, perishables tracking, and healthcare.
A good description, but we will translate their technology and approaches into understanding the process of change and reform in terms of DoD approaches to supply chain management and the possibilities when applied to a large global program such as the F-35.
Photo credit: Petty Officer 2nd Class Cyrus Khemalaap, a native of Palisades Park, N.J., checks containers of ammunition as they are loaded on trucks to go to the ammunition supply point.
The 1st Sustainment Command (Theater) munitions section was responsible for the distribution of the ammunition that comes in from a port in Kuwait as seen in this 11/26/07 photo.