2015-03-04 By Robbin Laird
The F-35 program has been built around a very different manufacturing model for fighter jets, more modeled on what an Airbus would do than the more traditional station build approach.
The F-35 is to be built on three final assembly lines (FALs)– Fort Worth, Cameri, and next year in Japan.
The line in Fort Worth is a pulse line, meaning the planes move on the line through their full build. Currently, the planes move, about five days through the line during their 20 months on the line. Three configurations are built on the single line – F-35As, Bs, and Cs – as well as modified allied versions of those aircraft, such as the drop chute on the Norwegian F-35A.
The aircraft is built on a digital thread foundation, meaning that digital systems are crucial to the supply chain and component builds and for the final assembly of the components, as well as for the maintenance of the plane.
In an article which I wrote in 2009, I focused on the digital thread production system as a key element in how the program would unfold.
The F-35 is a hub-and-spoke system whereby the collaborative information sharing and engineering processes are co-located in the hub but closely connected to the stakeholders. A digital thread manufacturing capability enables the collaborative system.
In Digital Thread manufacturing the CATIA computer model feeds directly into a Computer Numerically Controlled (CNC) machining center, and Coordinate Measurement Machines (CMM), or is processed in a Composite Programming System (CPS) before being sent to the Fiber Placement Machine. In both cases the finished product can be traced back to the original computer model through a “digital thread” which ensures greater precision and accuracy in manufacturing.
The F-35 is a globally sourced product. The global sourcing is based on the basic manufacturing model for the F-35. Global suppliers are stakeholders in the digital thread manufacturing process and collaborative participants in a networked engineering approach to the development and production of the aircraft.
On my recent visit to the Final Assembly Line in Fort Worth in February 2015, I had a chance to talk with Don Kinard, an expert on F-35 manufacturing, at the plant.
This was a follow up from an earlier discussion I had with Kinard during my last visit to Fort Worth which was in November 2012.
The production line and the manufacturing process has matured during this period and we discussed the maturation and its significance for the way ahead.
There is a whole lot of discussion and political maneuvering around the F-35, but underlying the program is a fundamental production reality – a 21st century production process, one final assembly line built on pulse manufacturing, and two others either using or about to use a station built approach.
This process has built into a maturation dynamic, which improves quality, effectiveness and efficiencies, as well as drives down costs.
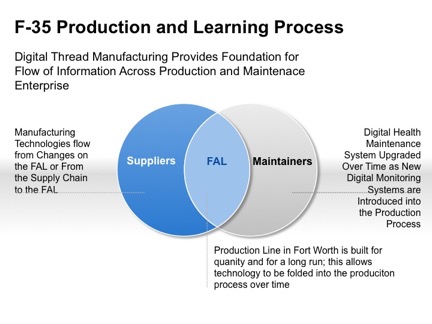
Additionally, the learning process from suppliers to final assembly to maintainers is a fundamental part of the F-35 effort. The first military aircraft program to be built in numbers built on a digital foundation, the F-35 has an inherent learning process built into it through which digital communications provide feedback loops and shaping learning curves as well.
The numbers side of this important – as a supplier in Australia, the CEO of Quickstep put it:
“The F-35 is the military equivalent of the A-320 in terms of populating the fleets of global users.”
Numbers matter crucially in another way, namely in terms of supply chain investments and ramp ups.
Without long lead time numbers, suppliers will not invest in the ramp ups necessary to deliver a steady flow of aircraft, a flow which is on the uptick as well.
Lockheed is a 30% both participant and final assembler of the program; the other 70% are the suppliers and tool manufacturers who are key stakeholders. The suppliers come from the U.S., the global partners and FMS partners.
Question: What is different with regard to the production line since I last was here?
Kinard: One thing is that the promise of significant production of F-35s for foreign customers is being realized. In the period ahead through 2020, nearly 50% of the jets coming off of the FAL will be foreign bought. Right now you will see two Israeli jets, two Norwegian jets, several Italian and UK wings on the line.
It’s really quite remarkable the response we’re getting from the other countries. And we build them and they’re all a little bit different. They’re not exactly the same, but our system handles that little bit of that variation that we get from different country requirements.
That’s the whole flexibility of having a single production line that builds three different variants already.
If you put another small changes in each of the variants for the different countries it doesn’t really disrupt the line significantly. We delivered 35 in 2013, we delivered 36 in 2014; and the JPO has asked us to deliver 45 this year including one aircraft from the Italian FACO.
And then it’s simply the process of building the airplane.
We had this conversation a little bit differently a couple of years ago, but building the aircraft isn’t a mystery anymore.
We have the tools, we set up a FACO, we set up a wing line in Italy. We set up a FACO in Italy that’s producing. We’re setting up the first load for the Japanese FACO is December.
And that just speaks again to the maturity of the manufacturing system in general.
What we’re working on is polishing that system because we’re going to cut the hours per unit by another 50% before we get to rate production in the next three years.
We have already cut it by 65% since we started building production airplanes; we’ll cut it another 50% before we get to rate.
And that’s through things like working on the supply chain and on the maturity of the design, doing corrective action for some of our non-conformances which I would say a normal part of building the airplanes in general and the general learning curve in manufacturing.
Question: For the suppliers, seeing production in growing numbers coming out of the plant is a crucial indicator that they need to invest in their efforts as well.
How do you see this aspect?
Kinard: That was one of the biggest issues early on because some of our suppliers had made investment and the rates just went over to the right.
Now that they see the long lead money is starting to come through they are investing.
For example, we will receive our first Israeli wing boxes in the summer. They’re building the outer wing boxes. We will receive our first Italian wings, full-up wings also around summertime.
And so all of those programs are now starting to gel for capacities.
We have our third or fourth Turkish center fuselage already delivered. So that international plan is also going well.
Again, all of that speaks to the maturity of the manufacturing system that we can build centers in Turkey.
And we have built our first vertical tails at Marand in Australia under the guidance of BAE..
https://www.sldinfo.com/marand-australia-celebrates-first-australian-f-35-vertical-tail-delivery/
Question: The supply chain and the FAL are inextricably intertwined in delivering airplanes.
How does the long production run affect the ability to fold in technological innovations across the production process?
Kinard: With a long production run, we can focus on folding relevant technological innovations to improving efficiencies on the production line.
For example, when you were here last, we had not installed a new technology on the line called structured light.
With the structured light system we can get a 3-D image of the airplane and scan the airplane and compare the model being built with the 3-D data in Catia.
It significantly improves the comparison of the as-built to the as-designed, and helps us troubleshoot problems a lot faster.
Instead of doing gap measurements where you do a lot of individual gap measurements all over the airplane, we will eventually scan the airplane.
Unlike with the F-22 which was a production run of a relatively small number of aircraft, the F-35 because of the production runway in front of us, we have the potential to implement lots of technologies to help us reduce the costs even more.
Digital thread is a big player in making significant differences to the way we build the airplane.
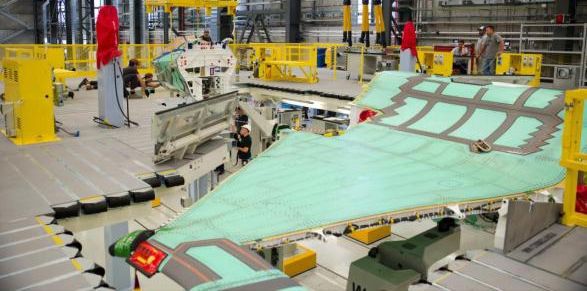
Question: What is the impact of having two other national approaches to final assembly?
Kinard: They see things differently.
The Italians have seen the way we build the airplane and we see how they build the aircraft.
Technically we build the aircraft the same way but improvement ideas come from all of the participants.
I’m the collector of those lessons learned from all the sites and so it’s been real interesting to see the feedback we’ve received.
One of the strengths of the program from inception was the incorporation of technology and knowledge from all of the partners.
Of course, the Italians and Japanese are building a lot different quantities than we are.
The Italian FACO is going to be two a month, the Japanese FACO is going to be at most one a month.
With those kind of numbers, they’re not doing it exactly the way we are. They’re not going to have a pulse final assembly line, for example. They’re probably going to have a station build line, but those are all things that you would do.
Our line is established for quantity build and if I was building one a month I might not pulse them either as it costs money to move them.
But overall, we are now in the manufacturing phase, which I might call, taking it to the streets.
Meaning we’re taking a digital thread to the workers on the floor. And moving forward as well we’ll eventually take this right to the maintainers.
A lot of things we’re doing in a production floor will eventually be a bonus for the maintainers who work on the airplane.
For example, we can set up a portable optical projection system, and one can project work instructions directly onto the airplane that he’s working on.
The fidelity of what he sees and can focus his attention on is ramped up.
The interactivity among the suppliers, the FAL and the maintainers is much simpler because we can talk to each other from long distances away using the digital thread too.
And changes in the production process software are already cross-fertilizing with the maintainers.
For example, in the transition from LRIP-5 to LRIP-6 software, we introduced more functionality into the Prognostic Health Management (PHM) system.
We then used the PHM improvements in the production process to get what we call network status of for our combat mission systems.
From a production point of view, we get a lot of information as we’re building the airplane in terms of how well every system is working.
And the PHM is going to continue to get better as we go through the different software lots as well.
The software changes have helped the pilot, but it’s also helped us build the airplane because we were historically using very manual techniques to go troubleshoot problems.
With the software enabled process and airplane, we have significant situational awareness (SA) of the airplane, not just for the pilot flying the airplane but for the supply chain, the FAL and the maintainers.
Question: So you are saying that the software that you’re improving for understanding any problems you have on the production side translates directly into improved maintenance software?
Kinard: Absolutely.
It was the same kind of thing that the maintainers will use and be able to download, troubleshoot the airplane quicker.
That was, of course, that’s one of the mantras of joint strike fighter was being able to have a maintenance system that allowed you to not only save cost but to improve awareness both from a pilot point of view as well as from maintainer’s point of view.
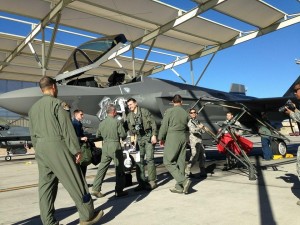
Question: As you mature the production process, you are looking to enhance automation in that process.
How does folding in automated processes work?
Kinard: For example, we did not utilize automated drilling on the F-22. It was a fill and fare process for finishing as well.
We now do probably 20-25% of our hole drilling on the F-35 with automated systems.
There’s even a new auto-drill going in right now which illustrates how we continue to look for ways to do automation – because it really is faster, it really is more accurate, and it takes away a lot of the manual stuff that takes experts to do.
The advantage to the new auto drill it’s got all the new gadgets on it. The new drill uses a minimum quantity lubricant for doing the auto drilling. It also has automated measuring of the holes. So I actually drill the hole and measure it at the same time.
And that way I can keep track of quality even better.
You wouldn’t think drilling holds is a big deal, but drilling holes is a big deal in an airplane to get 99% yield, perfect countersink depth.
Question: There have been many critics of building a common aircraft for all three services, for example RAND published a report a few years ago saying it would have been better to have three different airplanes.
From your point of view, what is the advantage of commonalty for a production process?
Kinard: The volume of aircraft allows us to improve the production process on a single line.
We are on the 70th F-35A, the 51st F-35B and on the 25th F-35C; this allows an ability to deliver efficiencies and cost savings that if they were not common would not easily happen.
The mission systems are 100% common; the airframes 70% common.
Because of the commonality in the mission systems, we know how to troubleshoot the systems almost independently of the type version we are building.
The guts of the airplane, mission and vehicle systems are very common.
It helps us put it together and it certainly is going to help the customer maintain it in the future.
Question: The F-35 program is unique but it is having a significant impact on the supply chain and the entire aerospace industry.
How would you describe its ripple effects?
Kinard: Remember we buy 70% of the airplane from somebody else. One of our initiatives right now and it’s been for a while is to take what we’ve learned and distribute it to the industry.
This is a stealthy aircraft, but more than being a stealthy aircraft this is a very aware aircraft.
If you look at situational awareness on this aircraft there’s nothing like this ever in terms of what the pilot is able to understand about his environment and his surroundings. The sensors on the aircraft are amazing,
But if you really think about the way this aircraft, it’s not just the stealth that gives us the advantage as much as the avionics and the situational awareness.
With regard to production we have learned a lot about how to precision tool an advanced aircraft. The companies that are doing the machining for us are the high-precision machining are German machines and Italian machines.
So we have learned a lot about how precisely to control the configuration of an aircraft.
We have learned a lot about how we apply digital thread in an environment such as getting 3-D drawings directly on the factory floor; technologies for being able to interact with a tablet directly with the 3-D data from the airplane, which is a real time interact.
The ability to measure as I build, the ability for a mechanic to have it automatically verify the configuration, verify the quality, simply because I have this ability to compare the as-designed to the as-build directly is built into the evolving process.
We are building in augmented reality innovations, and we’re looking at all the innovative ways for putting information in front of the pilot, the line worker, and the maintainer. We do it for the helmet already. The pilot gets amazing information in the helmet. Clearly, the same kind of capability works for mechanics.
Whether it’s a google glasses kind of approach or whether it’s a tablet kind of approach those technologies will continue to proliferate. A lot of companies are looking at that technology. We’re certainly looking at it a lot.
But again remember, we also need it for the supply chain. And everything, almost everything I’ve mentioned has some impact on the maintainer community whether it be how the maintainers get their instructions, how they repair the airplanes, how they diagnose the airplanes, that’s all part of the same innovation.
In other words, it is a highly interactive process of innovation among the suppliers, the final assembly lines and the maintainers in reshaping the combat capabilities of the F-35 as a global enterprise.
Note Regarding the Slideshow:
Visiting the FAL in Fort Worth highlights the process of moving planes from one end of the assembly line to the other over a year and a half.
The planes move on average every five days, and the process of building aircraft is clearly accelerating.
The result will be seen in the numbers of deployed aircraft in the period ahead, more than 600 by 2020.
In the second photo, the numbers of aircraft – more than 400 – deployed in various global locations by 2018 is portrayed.
During my visit, I saw several partner airplanes on the line including British, Norwegian and Italians, and there may have been more but that is what I saw while visiting the FAL.
And the numbers are clearly ramping up for all three models, and note BF-51 which is the 51st STOVL jet, as I was touring the line.
The remaining photos provide various views of the line and aircraft in various phases of production.
The photos towards the end of the slide show highlight planes at the end of the production line or in the paint shop.
The photos were shot by Angel DelCueto, Lockheed Martin photographer, on February 20, 2015 and were subsequently cleared by the Joint Program Office.
And see the recent story by Steve Trimble of Flight International about his recent visit to the FAL as well:
https://www.sldinfo.com/an-update-on-the-f-35-final-assembly-line/
As Trimble put it in his article published on January 22, 2015:
Mass manufacturing and stealth aircraft have never mixed well. Hundreds of thousands of parts must align at tolerances measured to the thousandths of an inch. A structural misalignment no wider than a few human hairs is enough to make an aircraft shine like a lighthouse in the electromagnetic spectrum.
In the elite club of stealth aircraft manufacturers, Lockheed Martin set the output record six years ago by averaging two F-22 Raptor deliveries per month, then topped that four years later as the F-35 Lightning II production rate reached three per month.
If Lockheed’s order projections are realized, however, the F-35 must become the stealth fighter equivalent of the Ford Model T in less than four years.
That is when monthly output at Lockheed’s mile-long factory in Fort Worth, Texas, is supposed to reach a peak of 17 F-35s in 2019.
Lockheed has built non-stealthy fighters faster in the past – the same factory built 33 F-16s in October 1981 – but the four-year goal for monthly F-35 deliveries is nearly seven times higher than any stealth aircraft program has ever achieved.