2017-05-31 In a recent article in The Manufacturer, there is a look at F-35 manufacturing in the United Kingdom.
It is the Typhoon and F-35, very much live MOD acquisitions, that offer the greatest opportunity – and imperative – for replacing parts that combine the daunting mix of intensive man-hour manufacturing with low lifetimes, with parts that can only be made possible by technologies that were invented long after either plane was a mere twinkle in its designer’s eye.
This article offers some illustrations of how BAE Systems has successfully deployed these new technologies in the search for greater efficiency, lower costs and longer operational lifespans….
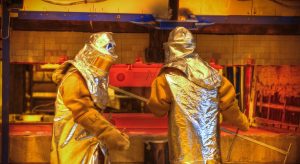
The article is well worth reading.
For example:
BAE Systems makes the rear fuselage of the plane, from just before the tail backwards, to include the two V-angled vertical tail-planes and the two horizontal tail-planes. There are 3,180 F-35s on order, so there is plenty of high-value work to be done in the coming years. The contract extends to a range of internal systems and post-production services.
There is something deeply impressive and simultaneously quite intimidating about the main machining facility. Sixteen Starrag 1250STC 5-axis milling machines dominate the space. Behind glass windows one can catch glimpses of the robotic arms sliding between the machine head and the tool storage to select the right one for the next phase of the job.
The titanium billets come in pre-cast by subcontractors, in rough form, ready for the fine machining that takes several hours per unit. No room is allowed for error, with tolerances of just 5/1000ths of an inch in the machining process, which drops to just 7/10,000ths of an inch during the assembly process. It is a financial as well as an engineering imperative – one intricate part of roughly 3 feet by 2.5 feet is dubbed the DB9, because one could buy an Aston Martin for the same money it costs to produce.
Just as with the Typhoon machining, human intervention is minimal….