When interviewing the CO of 2nd Marine Air Wing, Major General Cederholm underscored the importance of the logs and maintenance side of his command to be “ready to fight tonight.”
We operate all over the globe. Right now, we have forces all the way from Europe into the Far East, and everywhere in between.
“The sun never sets on 2nd Marine Aircraft Wing. We have to have a ready force and generate combat power today as we face the challenges of transformation tomorrow.
“We can never lose our readiness trait, or our ability to respond immediately when called upon.
“We’re looking at efforts right now to increase our readiness and our availability across fully mission capable aircraft, which is basically our no-go criteria when it comes to combat operations. The metric that matters to me is the availability of fully mission capable aircraft, not simply availability of an aircraft.
“When we send aircraft into harms way, we owe the aircrew and the Marine Riflemen, a fully mission capable aircraft.
“In this context, we are focused on increased reliability of parts and weapons systems. I have been focused significantly in my career on training; now I am laser focused on the logistics side as well.
“We are examining reliability across the parts for every type, model, and series of aircraft at 2nd MAW, and working with various institutions to improve reliability.
“Even if there are higher upfront costs to get reliability enhanced, it will be cheaper in the long run for the operation of a more resilient force, which is clearly what one needs when the demand is to fight right now, when the phone rings.”
There is little doubt then that the CO is welcoming the news from Fleet Readiness Center East.
As Kimberly Koonce of FRCE wrote recently in an article published January 29, 2021:
Every field of effort has a standard to beat. Track and field had the four-minute mile. For baseball, the bar is 762 career home runs. For the V-22 Osprey production line at Fleet Readiness Center East, there was the 300-day turnaround time for returning the aircraft to their fleet customers.
On January 15, the V-22 line broke that elusive 300-day mark when the team returned its most recently completed aircraft in 297 days, far below the negotiated standard of 420 days.
V-22 production supervisors have credited much of the decreased overhaul time to the line’s recent adoption of a team concept. Under this new way of doing business, one airframes work leader is responsible for each aircraft, with the assistance of subject matter experts in the sheet metal and electrician trades. Together, these three experts make daily decisions on scheduling, parts and staffing needs.
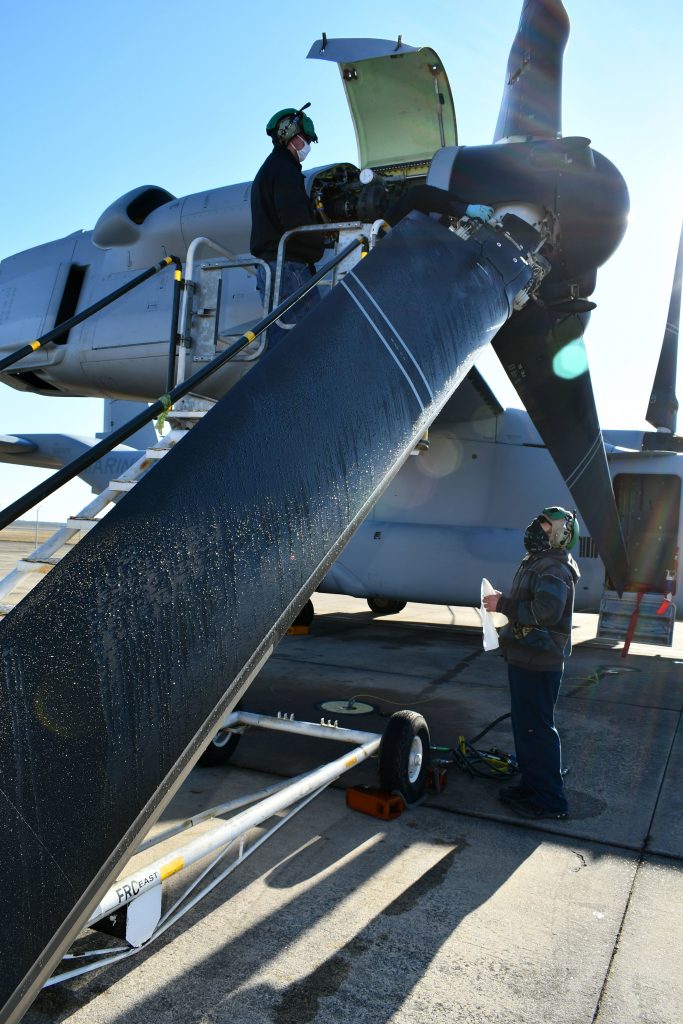
“What it did was give us a driving force, a person who really knows what needs to be done on the aircraft and what is required to complete that task,” said Don McLean, V-22 first-line supervisor. “At our daily morning briefings, the work leader shares the information with the team, and we assign artisans to work based on that day’s needs. It keeps us laser focused on the line’s priorities.”
Parts are getting the same attention as personnel on FRCE’s V-22 line. The team maintains a spreadsheet detailing required parts and when they will be needed in the process. Supervisors say this long-view approach helps the team overcome potential obstacles before they become work stoppages.
“We’re identifying long lead-time parts, and as we achieve our milestones on the aircraft, we can look ahead and say we need this, when can we get it? And if we can’t get it, how can we overcome that obstacle?” said Matt Sinsel, V-22 production control coordinator. “We may have to find an engineering solution, locally manufacture a part, or take the part from another aircraft. We work through our obstacles to keep aircraft on track.”
Program leaders have predicted that turnaround times of less than 300 days will become more common on the V-22 line in the near future, due to improved parts availability and increased staffing of aviation professionals. The line’s ultimate goal is to meet the fleet’s demands for aircraft in 250 days. Andrew Rock, FRCE V-22 branch head, said that goal is attainable by working with the Defense Logistics Agency and the Naval Supply Systems Command, as well as applying more aviation maintenance professionals to each aircraft.
“Our negotiated turnaround time with Naval Air Systems Command is 420 days, but our target turnaround time to meet fleet demand is 250 days. There’s a huge difference in what the negotiated demand is and what we are now being asked to do,” Rock said. “Obviously, in order to do that, material must be available when it is needed and you have to apply more manpower, so we are currently in a ramp up to get the manpower on board, to get them trained, and then, regardless of the material condition of the aircraft, I think 250 days is attainable for most aircraft.”
The line’s achievements have not gone unnoticed by senior leadership at FRCE. Col. Thomas Atkinson, FRCE executive officer, visited several shop areas to thank the people whose efforts contributed to the milestone.
“The difference between the planned turnaround of 420 days and 300 days is about four months. You’ve done this four months faster than you were expected to,” said Atkinson. “You’ve given one third of an aircraft back to the Marine Corps. We do that three times, that’s like having an extra aircraft that doesn’t have to be purchased and that can be used for training and other missions.”
Supervisors said the new team concept and the success it has produced has energized employees working on the V-22 Osprey, and they predict the team will shatter other milestones in the future.
“This achievement tells me the entire V-22 team has bought in,” said Rock, crediting the artisans, estimators and evaluators, quality assurance, production controllers, and local manufacturing with contributing to the program’s success. “The entire team takes pride in what they do. Everyone is determined to meet all the goals this command throws at them, and so far they have done it.”
FRCE is North Carolina’s largest maintenance, repair, overhaul and technical services provider, with more than 4,000 civilian, military and contract workers. Its annual revenue exceeds $1 billion. The depot generates combat air power for America’s Marines and naval forces while serving as an integral part of the greater U.S. Navy; Naval Air Systems Command; and Commander, Fleet Readiness Centers.