2015-03-20 By Robbin Laird
During my first visit to the Final Assembly Line of the F-35 since 2012, I was able to visit the line and see a number of changes.
I also had a number of interviews which provided updates as well.
The first interview with Dr. Mike Skaff, the chief engineer for the Pilot Interface Integration or for non-acronym lovers, the man responsible for leading efforts to provide better ways for information to be presented to F-35 pilots, a capability which current F-35 pilots have been very enthusiastic about.
A second interview was with Dr. Donald Kinard, the well-known F-35 manufacturing specialist, who discussed the evolution of the manufacturing process and its maturation.
This was an update from my last interview with him in 2012.
A third interview was with the head of Naval programs at Fort Worth, the former CO of the USS Harry Truman, Jim Gigliotti.
The focus there was upon the cross-cutting processes of US Navy fleet innovations with the coming of the F-35C.
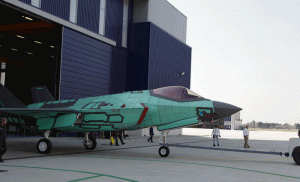
The final interview was with Steve Over, the head of international Business Development for the F-35.
In this interview, Over provides an overview (sorry for the pun) on the F-35 program circa 2015.
My initial take on what I saw and heard in Fort Worth was encapsulated in an earlier article:
I had not visited the Final Assembly Line or FAL in Fort Worth since late 2012.
Much has changed as the line has matured, and a line stood up in Cameri, Italy and one being built in Japan.
The first Italian FACO F-35 rollout will happen soon in Italy.
A key aspect of the program is the joint buys of the US services and the partners in common contracts with Foreign Military Sales customers like Israel, Japan and South Korea purchasing via the FMS route.
The F-35′s nine partner countries are Australia, Canada, Denmark, Italy, the Netherlands, Norway, Turkey, the United Kingdom and the United States.
Nearly 50% of F-35s to be delivered in the next five years are for international customers.
Currently, F-35s are flying on nine operating bases with 130 airplanes flying and the fleet as surpassed 29,000 flight hours.
There are 88 jets under construction at the Fort Worth plant, and one can see already on the line jets being built which will surpass the numbers of F-22s which were built.
A single line is building three different variants of the aircraft – the F-35A, the F-35B and the F-35C – and can accommodate configuration differences for the allies, such as the chute for the Norwegian F-35A, which is being built to deal with icy runways.
The discussion with Over provided a number of additional details and elements for understanding the state of play for the program as of February 2015.
The first point was with regard to the planes under contract and anticipated to be under contract by the Fall of 2015.
We are starting to deliver LRIP-7 airplanes and are fully under contract for LRIP-8 airplanes.
We are under contract for long lead airplanes for LRIP-9 and we have submitted a proposal to the US Government for both LRIP-9 and LRIP-10 and their intention is to negotiate both contracts simultaneously.
It is anticipated that those contracts will be concluded in the Fall of 2015.
The buying process for F-35s is unique in many respects.
The partners and the US services buy in common.
The Foreign Military Sales (FMS) customers have separate contracts, which are concluded separately, and then the FMS aircraft folded into the single production run process.
The partners actually join in and procure their aircraft along with the US government through the Joint Program Office.
The JPO then takes those along with FMS buys and authorize aircraft within individual LRIPs.
In effect, the partners and the services are integrated into a single buying process.
Clearly, the F-35 enterprise is focused on U.S. Services IOC’s which start with USMC in July 2015, the USAF in 2016 and USN in 2018.
The Marines have the software, which they will go to IOC with currently, and will finish testing this year, including tests this spring on the USS Wasp.
By the end of last week, the USMC has 12 test points remaining and one additional weapons accuracy test to complete before finishing testing for IOC.
Early increment 3i software, which is loaded into a new generation of mission computer, is being tested now as well.
USN testing is continuing with the next carrier based testing to occur in the Fall aboard the USS Eisenhower.
During the recent USS Nimitz testing, the F-35C began its night operations testing, and this will continue along with weapons loading (inert) and other tests relevant to the work flow aboard a carrier.
And looking at numbers of aircraft, according to Over:
“We’re under firm contract, through LRIP-8 for over 230 airplanes.”
The projection is for more than 400 airplanes deployed by 2018.
And more than 600 deployed by 2020.
Not surprisingly, the price point of the airplane is coming down as the manufacturing line is maturing; the supply chain is ramping up and maturing, and the numbers increasing.
The price point according to Lockheed Martin is well on the way to reaching DoD’s estimate of $85 million for an F-35A ordered in 2019.
It will continue come down as a number of process improvements and new manufacturing technologies introduced into the supply chain and the final assembly line.
I would put it in the words of the PEO, Lieutenant General Chris Bogdan.
When he says, ‘in the 2019 timeframe we’re going to have a fifth generation airplane that’s less than or equal to the price of a fourth gen airplane,’ this is why he can make that statement with confidence.
When you look at that cost curve about 20 percent of that cost reduction comes just from learning how to build the airplane more efficiently.
Airplane after airplane after airplane will now come off of the line.
About 80 percent of that learning curve effect comes from the economic order quantity.
And of course, you can see that between LRIPs 4 and LRIP-7, the production quantities were held very flat and very constant.
So we were able to achieve this reduction of the learning curve just through learning efficiencies.
Beyond the standard manufacturing learning curve affects, Lockheed, along with their industrial partners Northrop Grumman and BAE Systems, partnered with the U.S. Government and introduced “Blueprint for Affordability.”
The focus is to deliver an F-35 that’s less than $80 million in 2019.
By investing shareholder’s money in improvements up front, this will drive down costs further as it is rooted in process improvements and introductions of new production technologies, in both the supply chain and on the final assembly line.
These improvements aren’t going to increase the operational capability; these are going to make the airplane cheaper to build.
We’re investing $170 million over the next two years, this year and next year, in these modifications that will make the jet more easily produced.
It actually will occur at all stages in the supply chain.
It’s not just here in our facility.
It’s not at just in Northrop Grumman and BAE’s facility; we’re investing in projects that are even lower in the supply chain that will increase their ability to produce parts that are equivalent in quality but cheaper.
The five-year investment is designed to shave $10 million off the airplane by 2019, resulting in less than an $80 million jet. 131 production ideas so far have been submitted, 58 have been approved with $49 million investment.
Already, we can directly tie $260,000 per jet lower price associated with the LRIP-8 jets.
And when you look at how this compounds year over year, through LRIP-11 we project a $2 million reduction in the price of the basic jet.
The briefing illustrates the points made above and provides highlights for the program in 2014 as well as projected achievements in 2015.
Note Regarding the Slideshow:
Visiting the FAL in Fort Worth highlights the process of moving planes from one end of the assembly line to the other over a year and a half.
The planes move on average every five days, and the process of building aircraft is clearly accelerating.
The result will be seen in the numbers of deployed aircraft in the period ahead, more than 600 by 2020.
In the second photo, the numbers of aircraft – more than 400 – deployed in various global locations by 2018 is portrayed.
During my visit, I saw several partner airplanes on the line including British, Norwegian and Italians, and there may have been more but that is what I saw while visiting the FAL.
And the numbers are clearly ramping up for all three models, and note BF-51 which is the 51st STOVL jet, as I was touring the line.
The remaining photos provide various views of the line and aircraft in various phases of production.
The photos towards the end of the slide show highlight planes at the end of the production line or in the paint shop.
The photos were shot by Angel DelCueto, Lockheed Martin photographer, on February 20, 2015 and were subsequently cleared by the Joint Program Office.
And see the recent story by Steve Trimble of Flight International about his recent visit to the FAL as well:
https://www.sldinfo.com/an-update-on-the-f-35-final-assembly-line/
As Trimble put it in his article published on January 22, 2015:
Mass manufacturing and stealth aircraft have never mixed well. Hundreds of thousands of parts must align at tolerances measured to the thousandths of an inch. A structural misalignment no wider than a few human hairs is enough to make an aircraft shine like a lighthouse in the electromagnetic spectrum.
In the elite club of stealth aircraft manufacturers, Lockheed Martin set the output record six years ago by averaging two F-22 Raptor deliveries per month, then topped that four years later as the F-35 Lightning II production rate reached three per month.
If Lockheed’s order projections are realized, however, the F-35 must become the stealth fighter equivalent of the Ford Model T in less than four years.
That is when monthly output at Lockheed’s mile-long factory in Fort Worth, Texas, is supposed to reach a peak of 17 F-35s in 2019.
Lockheed has built non-stealthy fighters faster in the past – the same factory built 33 F-16s in October 1981 – but the four-year goal for monthly F-35 deliveries is nearly seven times higher than any stealth aircraft program has ever achieved.