2013-10-30 By Robbin Laird
During a visit with Ed Timperlake at Yuma USMC Air Station and then at the Lockheed Martin Fort Worth F-35 facility, Ed and I had a chance to discuss the Cameri F-35 effort with two young Lockheed Martin Aero officials involved in that effort.
We sat down with Brian White and Kris Yowell in late 2012 to discuss the FACO and its significance.
Brian White is a relative newcomer to the program but with significant background in international business with Lockheed Martin. He has been the Lockheed official responsible for the execution of the contract for the FACO from the Lockheed side.
Yowell has been with Lockheed since 1986 and the JSF program since the start of SDD production. He has worked within production and global supply chain within the program and has worked with the Italians for the past five years living in Italy for 3.
The two have brought significant international and production experience to the working relationship with the Italians.
https://www.sldinfo.com/the-italian-f-35-faco-a-key-asset-in-the-global-f-35-support-system/
While I was visiting Cameri in October 2013, the two had just come back to the facility, and I had a chance to sit down with them again to get an update on the past six months from their perspectives.
In the discussion, which followed with White and Yowell, several key themes were emphasized.
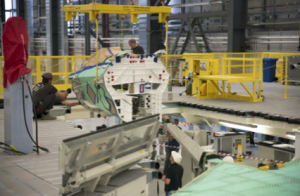
First, June 18, 2013 was an important date in Cameri history. This was the day that the first F-35 to be built at Cameri began its assembly process.
Second, the year ahead will be challenging as the ramp of production continues, the wing assembly process accelerates and as the first planes prepare to be flown and put through the acceptance process.
Third, there has been significant cross-learning within the program between Fort Worth and Cameri, and with the addition of the Japanese this process will continue.
An example was cited of how the Italians have improved on the automated drilling process for wing Outer Wing Boxes, being able to simplify the process by dry drilling which demonstrates new possibilities to Fort Worth as well.
Fourth, the Japanese have visited the plant to learn how a Cameri-sized facility might be built in Japan, for such a facility is clearly closer in scale to what Japan itself will do.
The complexity of the multi-year process of setting up the plant was highlighted as well for both the American and the Italians. The process had to be shaped for export, the machine tooling products put into place, the production processes installed and the teaching of the processes commenced and honed.
The learning at Cameri with regard to wing production is important as well in two ways. First, the Cameri process is producing high quality wings for the entire F-35 program and second, the stand up of this facility will help in learning how to set up the wing facility in Israel as well.
In effect, the Cameri plant demonstrates to important developments with regard to the F-35 program.
First, the production processes have matured to the level whereby they can be transferred.
Second, that the production processes can indeed by transferred and a new line established in a completely different geographical and cultural area.
The Italians also have the advantage of closer geographic proximity for their supply chain so that the Cameri plant can shape a supply chain to support the plant in close proximity to the plant as well.
Technology transfer is not simply about technology; it is about business processes and models as well. And this is not a one way but a two way street, as a global manufacturing system is set up within the F-35 program. It is not just about a global supply chain; it is about global system providers and global manufacturing, meaning manufactured outside and inside the United States.
The full benefits of such a process are only beginning.
As the ramp up of production occurs, and the cross-learning is allowed to reshape production processes more effectively, not only economies of scale but economies driven by process innovation will occur.
This is clearly the benefit of having a global program built around a plane with more than 80% commonality built into its three variants.