2015-05-31 By Robbin Laird and Murielle Delaporte
During the visit to the Boeing V-22 Osprey factory at Boeing’s Philadelphia site, we had a chance to sit down with the Vice President of Boeing Tiltrotor Programs, Kristin Robertson.
Prior to her current role, she was the Deputy Program Manager of the T-X Program, a part of the Boeing Military Aircraft (BMA) business unit of Boeing Defense, Space & Security.
T-X is a comprehensive training system or Family of Systems (FoS) designed to replace the USAF’s fleet of T-38 Talon training jets.
Previously, Robertson served as Director of Direct Attack Weapons Programs, a division of Boeing Missiles and Unmanned Airborne Systems (MUAS). Programs within her portfolio included the Joint Direct Attack Munition (JDAM), Small Diameter Bomb (SDB), and the Countermine System.
Question: Having visited the plant and watched the evolution of the Osprey in combat over the past few years, it is clear that the plane is maturing.
Could you talk about your sense of where that manufacturing process is at this point in the program?
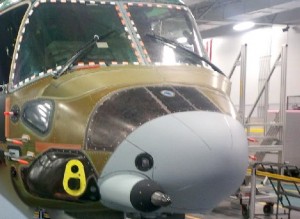
Kristin Robertson: With nearly three hundred aircraft under our belts, we credit process discipline as an enabler to support a stable configuration for the aircraft.
For example, we have implemented a number of lean manufacturing processes that drive repeatability, standardization and standard work, which have enhanced affordability.
And we have implemented innovative ways to achieve seamless and repeatable production.
Using 3-D model based definition, we are able to work on new configurations of the aircraft, which can fit, into the mature production process.
We also see a maturing of the supply chain, which can enable an effective way forward as well.
Question: The V-22 is very dependent upon composites, and you have drawn upon your commercial as well as military work to mature your composite production process.
Could you discuss this aspect of the program?
Kristin Robertson: A significant portion of the aircraft is composite.
Over time, our engineering and tooling have evolved. Automated, state-of-the-art tooling drives quality and repeatable manufacturing process.
Question: We are a turning point with regard to the aircraft, both in terms of international sales as well as new multi-mission variants.
What is your perspective on this opportunity?
Kristin Robertson: Although we do not define our customers’ concepts of operations, we are positioned to support those efforts as they evolve.
Roll-on and roll-off capability such as aerial refueling is a case in point.
We work with our customers to drive our investments and the technologies, and try to bring those to bear, to ensure that our customer has the capabilities that support that future vision of cooperative operations or changing CONOPs.
We think the architecture of the aircraft, the physical architecture, the computing architecture and how it all operates together is certainly a key enabler to any future capability.
As an industry, we’ve been investing in new architectures and new capabilities to help support a more rapid insertion model.
Question: As you face the possibility of global sales, it is important to get the global supply chain right.
How do you see this challenge?
Kristin Robertson: With global sales, we are currently working through FMS mechanisms and leveraging the current/follow on multiyear program..
Longer-term support agreements provide greater flexibility for industry and government from both a production stability and product perspective.
This approach drives affordability and leverages a stable product line.
This is the fourth piece in our Osprey series.
For the first three pieces of a six part series see the following:
https://sldinfo.com/osprey-at-the-eight-year-mark-preparing-for-the-next-phase/
https://sldinfo.com/the-next-phase-for-the-v-22-multi-missionization/