2016-06-06 A look at the new CH-53K is provided in a set of interviews with the USMC.
The article is based on interviews with:
- Colonel Paul Fortunato, Branch Head, Weapons Requirements (APW-1)
- Colonel Hank Vanderborght, Program Manager, PMA-261/H-53 Heavy Lift Helicopters
- Major Thomas Trimble, Heavy Lift Requirements (APW-51), Department of Aviation, US Marine Corps.
As Germany is looking for a successor to his CH-53 G the two US helicopter builders Boeing with its Chinooks (CH-47F) and Sikorsky with its CH-53s (CH-53K) are competing for the bid.
The verdict is planned to occur at the end of the year with a contract set in 2018 and first deliveries starting in 2022, while both could be picked for different missions and timetables according to some sources.
(See: Lars Hoffman, Germany Picks CH-53K, CH-47F as Options of New Helo, Defense News, January 26th, 2016 ; CH53K « King Stallion » et CH-47F « Chinook » pour l’Allemagne? Avia news, http://psk.blog.24heures.ch, May 17th, 2016 ;Defense Industry Daily (DID), CH-53K: The US Marines’HLR Helicopter Program, May 18th, 2016 ;Defenseworld.net, Germany Requests Princing For 41 CH-53K Choppers, May 18th, 2016 ; Franck Colucci, Testing Kings, Vertiflite, January/February 2016, page 19.)
The Luftwaffe wants to replace its old heavy-lift helicopters to perform MEDEVAC, personal recovery mission and support Special Forces.
The K, due to enter into service in 2018-2019, would almost double the gross take-off weight from 19 tons to 40 tons and benefit from a grouped order with the UMSC.
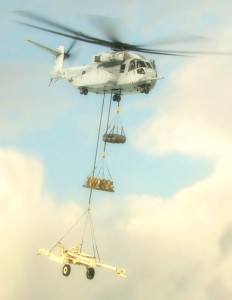
The U.S. Marines have indeed decided to acquire 200 of them: in their case, the King Stallion would triple the payload of the existing « Echo » super stallions, which are in great need for replacement given a usage rate triple the norm over the past years.
The attrition is high and there are no flyable spares available. The flight hour for the 15-year old CH-53E costs 20,000 dollars and the maintenance man hours: flight hours ratio has reached 44:1.
This is also the reason why maintenance and sustainability have been at the heart of the Integrated Test Team currently working on the Next Generation Chopper.
This ITT is divided between the Sikorsky Development Flight Center in Florida and the Naval Air Weapons Center Aircraft Division Patuxent River in Maryland and includes USMC maintainers
According to the three Marines interviewed in this article, who are centrally involved in the program, the CH-53K is a XXIst century air system, which will add significant capability to the evolution of the US Navy amphibious fleet for two reasons: its capacity for more efficient heavy lift and its ability to deliver loads to multiple points in the battlespace, faster, and with significantly enhanced integration with the other combat assets.
The hope is that, given this larger capacity and its potentially improved supportability, greater sortie rates will be generated significantly reducing the transit time to move supplies from the ship to the shore.
Just how the capabilities of the new aircraft would intersect with the evolving operational approaches is discussed in the interview below.
How important has it been building in maintainability to the CH-53K design approach?
It has been central from the beginning.
We formed a maintainer working group at the outset as part of the design team, which has met every quarter to provide their recommendations from a maintainer’s perspective with regard to ways to improve the design from a maintainability and sustainability perspective.
Currently, we have ten maintainers at West Palm working on the aircraft.
These are the seed corn for the new maintenance approach working with the new aircraft.
Their recent fleet experience has prepared them to act as a critical link between engineers and end users in the development the helicopter and the knowledge they gain during their time on the program.
We are counting on these Marines to reenlist and be our Staff Non-Commissioned Officers assuming leadership roles as future Quality Assurance Representatives and Division Chiefs of the first King Stallion squadrons.
Even though the aircraft is quite different, we wanted that field experience built into the design process from a maintainer’s perspective.
The team working the new maintenance approach are the future stakeholders and their ideas are incorporated into the design, as for example:
- On the CH-53E, when you have to work on, or replace, the fuel cell, you have to do so through big trap doors on the top of the aircraft. And then one has to wait a couple of days to have the gas free environment on which to work on the cell. A maintainer suggested that we build a port on the bottom of the K where one can access the fuel pumps directly and easily, and then if you have to change the fuel pump inside the tank, you could go underneath the aircraft, unscrew it, pop in a new one, connect it and off you go. You don’t have to wait until a gas free engineering environment is ready. There are several examples of this kind of input to the design of the new aircraft, which will enhance maintainability, which, in turn, enhances readiness and sortie generation.
- The design of the avionics systems is built around an avionics box for easy access to the cannon plug and wires, which the maintainers need to work on. Instead of having to have a flashlight, a mirror and another Marine holding something to get behind the systems, the systems are facing the maintainer directly for their attention.
The NAVAIR process is somewhat like a V where one side is design and the other is testing and fielding.
We are now largely past the design piece and we are now focused on test and aircraft performance under those test conditions. The ten maintainers that are down at West Palm are actually maintaining the aircraft.
They are validating maintenance procedures, while identifying best practices, while noting and correcting any discovered deficiencies .
The airplane is much more digital; and so are the maintainers; there is an evolving fit between the 21st century aircraft and the 21st century maintainer.
They are shaping the integrated manuals we need to support the aircraft in the field.
They are going to make sure that the manuals are written correctly.
That is why it so crucial to have the maintainers down at West Palm and integrated into the process from the outset.
Composites are now a norm for new air systems, as opposed to when the E was conceived: how does the evolution of the material technologies affect the K?
By leveraging modern engineering practices and materials, we have enhanced performance. The structural strength of the aircraft provides for extra performance, and is clearly a key reason why the K can lift three times more than the E externally in the same ambient conditions.
It is obvious, but important to underscore that a heavy lift mission is just that and that it does lead to stresses and strains on the aircraft as well as on the airframe.
The plane has been designed to take the stress of a three time enhanced lift capability and we are testing the aircraft rigorously and robustly to ensure that the performance is being met.
Even though the King is 5,000 pounds more on max weight than the Echo, it is able to fold down to a smaller footprint shipboard and can land on exactly the same ships as its predecessor.
Such capability stems from the conjunction of three technologies:
- the new engines (the GT-408) providing the lifting power;
- the split torque gearbox generating the power to the blades from the engine;
- the new all composite rotor blades with anhedral tips.[ref] The Sikorsky S92 has Growth Rotor Blades with anhedral blade tips providing enhanced lift and reduced blade-vortex interaction. The reduced rotor diameter achieved using the modern anhederal blade design increases the helicopter’s maximum airspeed, because the rotor blades can turn more quickly whilst reducing retreating blade stall. (http://www.alamy.com/stock-photo-the-sikorsky-s92-has-growth-rotor-blades-with-anhedral-blade-tips-83536560.html)[/ref]
The avionics and the fly by wire system are a major shift as well from the E to the K. How will the new technology have an operational impact from your perspective?
We land in hostile environments and in degraded visual environments as well.
The new systems will have a number of impacts, one of the most significant is stable hover.
Because of the ability of the aircraft to hover assisted by technologies onboard, we can land the aircraft much more safely and in difficult visual environments.
Automation will assist it in managing the flight and let us focus much more on the mission.
There are two different flight control modes on the aircraft, PFCS and AFCS. During different missions, one can select different flight control systems that are optimized for those missions. The different fly by wire systems actually assist you in optimizing those systems for different mission sets.
The cockpit is a glass cockpit with five Multi-Functional Displays. They dramatically increase air crew situational awareness.
The fly-by-wire flight control system makes the aircraft a lot easier to fly and allows the crew to focus on what the MFDs can provide to shape mission effectiveness.
Safety and security are significantly enhanced.
We have had a lot of mishaps with the E because of low visibility and brownouts.
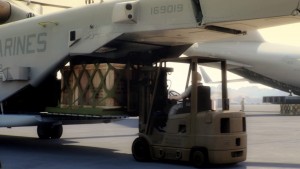
If, if I could compare the 53K, the 53K comes in to pick up an external load, there is a flight director in the aircraft, almost like an airliner.
And when you fly at the initial point, which is the last checkpoint on your route before the landing zone to pick up the external, the 53K pilot can push a button and the aircraft will fly itself to the load and basically come into a steady hover at a preselected altitude right over the load.
For example, if the pilot wanted that aircraft to go to 20 feet over the load, he would put those parameters in the system and hit the button and the plane will do that.
With regard to what we call “divided attention,” where you need to multi-task, the systems help you manage that as well.
For example, say you were inbound to a landing zone and you are about to come pick up an external load.
And all of a sudden you get a call on the radio that says: “hey, change your mission.
You now need to pick up the external and go to a different location and drop it off”.
Because the aircraft is so augmented and is able to do pretty much the pilots’ job, the crew can start re-planning that mission while one pilot can monitor the aircraft and the other pilot can actually re-plan the mission to go to the new landing zone.
Whereas in the Echo, it took the entire attention of the entire crew just to stay safe to pick up that external load in a difficult environment.
The power of the fly-by-wire system combined with the displays inside the aircraft makes in that sense the K much safer than other helicopters.
What are the assets of this next generation aircraft from a logistical point of view?
The K has two key features, which make it a next generation aircraft:
- The first is the widening of the cabin to allow it to load Air Force 463L pallets. Currently, when the Air Force arrives with a C-17 or C-5, we have to crack open the 463L pallets and re-palletize them into 48 x 48 wooden pallets and then put them into the Echoes. With the K we will be able to take them directly off of the C-5 or C-17 and roll the pallets right onto the Kilo and go to whatever FOB we need to deliver the cargo to. Logistical throughout will be much greater.
- The second is the triple hook system, which no other helicopter has. Whereas the E can only do a single and dual point, the Kilo can do a single, dual and triple point. The beauty of this capability is that we can be on an L-Class ship and pick up three independent loads. And then in one sortie, we can drop off those loads at three independent locations, which, from a logistical point of view, gives us much greater flexibility than we have ever had before.
The Echo was built in a former era when you brought supplies as part of a support wave; the K is being built in the age of force insertion across a distributed battlefield.
You can support three different company landing teams across the battlefield that could be supported by one ship, with three loads taken form the ship and then going to zone one, zone two and zone three without ever having to go back to the ship to reload.
This saves not only transit time, but exposure to threats, while flying the aircraft among multiple loadings rather than loading a triple package and taking off for the area of interest. You save sortie numbers simply by being able to use the triple hook system.
How has the Sikorsky approach to a Heath and Usage Monitoring System (HUMS) on its commercial helicopters affected the K program?
It is a crucial part of the program.
For example, Sikorsky has more than ten years of experience with the HUMS on the S-92, a helo that is flown three times as much as we would fly the K.
It is used for fleet management, and provides significant information with regard to the operational performance of the aircraft, parts and reliability and overall real-time data with regard to the operation of the aircraft.
We are leveraging this approach for the K and clearly when the E was built there was no HUMS system or capability.
An example from the S-92 world provides some insight into where we think the K fleet can go as well using the HUMS system.
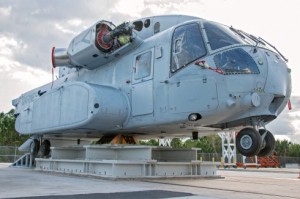
They’re measuring every aircraft across the fleet and they understand the signatures for every parameter they’re measuring looks like. So they understand what normal looks like and if something starts deviating from normal they can understand where the safety margins are.
One example that sticks in my mind was an S-92 that was flying for an oil company in the Singapore area doing globe plots. And they had a tail rotor gearbox in this aircraft that was showing some signs of wear and tear.
And they knew that the operator was going to need to have in about 20 flight hours dedicated base maintenance.
So before the operator even knew that there was something going awry with the aircraft, they called the operator and said : “ in this scheduled maintenance period, you need to change your tail rotor gearbox. By the way we shipped you a brand new one yesterday”…
We certainly look forward to such a capability within the K fleet.
In short, the predicate for the K is 21st century aircraft materials, systems and approaches.
The E was built in the age of the Studebaker; the K is built in the age of the electronically-enabled car.
In and of itself, that makes it a very different animal.
Editor’s Note: Recently, the French defense publication OPERATIONNELS SLDS published an article on the new generation CH-53K which was based on earlier articles published on Second Line of Defense.
This article is republished with their permission below and the PDF version of the article can be found below:
https://sldinfo.com/wp-content/uploads/2016/06/CH53K-as-published.pdf
The latest issue is being distributed at the Eurosatory international exhibition from 13-17 June in Paris and the OPS booth can be found in Hall 6 Stand 8A 350 at the show.
Eurosatory is a leading defence and security international exhibition which focuses on land and airland solutions.
The slideshow above shows the Commandant of the USMC visiting the Sikorsky CH-53K facility earlier this year.