2013-03-19 Second Line of Defense visited San Diego for the christening of the USNS Montford Point. The ship is the first of a new class of ships, the Mobile Landing Platform, and a contributor to the innovation in sea basing.
As Admiral Buzby, the head of the Military Sealift Command, underscored, the ship is part of a strategic revolution:
SLD: The innovation being generated from the support side is somewhat unusual and allows innovation on the mission side as well. How odd is it to think of the MSC at the cutting edge of change?
Admiral Buzby: It’s casting MSC in a little bit of an unusual role because historically, we get the cast offs from the Navy. We get 20 and 30-year-old ships that are held together with bailing wire and we keep them going for another decade or so. We also get purpose-built new ships, and that is becoming more the norm these days.
But now we’re finding ourselves suddenly on the very leading edge doctrinally, with brand new gear, with brand new concepts, with brand new con-ops to not only just follow, but to develop ourselves.
That’s requiring a bit of a reorganization within the MSC community to re-evaluate how we do various missions and how we produce the required readiness; it’s a very dynamic and exciting time for what has been a steady state outfit for a long time.
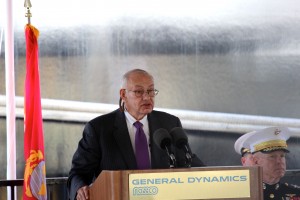
The ship also is part of an approach to building ships a new way. This aspect of the USNS Montford Point was discussed with Fred Harris, CEO of NASSCO, in his office on February 28, 2013 prior to the weekend christening event.
The first thing we discussed was the origin of the ship itself. As Jim Strock of the USMC Combat Development Command described it:
SLD: The ship, which we will see in March, is not the same as originally conceived. Could you describe the shift from original concept to the ship that is in the water?
Strock: The original Mobile Landing Platform was an entirely different ship under the MPF Future Construct and there was a complete capabilities document that was written.
There was a ship design team put together. We were in the throes of working the design when in the summer of 2009, the Department of the Navy made a conscious institutional decision to no longer pursue the MPF Future Construct but rather seek ways to enhance our current Maritime Prepositioning Ships program. A Tiger team was formed and came back with recommendations, which led to the current ship design.
When the NAVSEA PEO Ships came forward with a revised Mobile Landing Platform, that revised platform was downscaled significantly, but it preserved two essential seabasing capabilities.
The two essential capabilities that we wanted upfront was the ability to skin-to-skin marry to an LMSR at-sea, sea-state 3, come along side, tie those two ships together and then be able to move heavy rolling stock equipment up to and including tanks from the LMSR to the MLP. Secondly, the MLP would then be able to interface with LCACs to maneuver equipment ashore. It has been designed to provide for at-sea transfer of rolling stock at no less than sea-state 3.
In effect, it is a pier in the ocean.
https://sldinfo.com/adding-capability-to-the-evolving-seabase-the-coming-of-the-usns-montford-point/
Fred Harris added further detail to this crucial moment in which the ship was go or no go.
The Navy decided that the MLP was too expensive. They actually cancelled the program. But we took it on ourselves to argue for a more affordable ship with much of the same flexibility for much less cost, and giving them 80 percent of the capability they had before in the new design.
Some of the past ships have been designed to meet everyone’s requirement that anybody wanted. You ended up with ships that are highly capable, but sometimes are over-spec’d. And I think the Navy fully realizes that today
We have been in the forefront of a new approach. In my previous life, I ran the Virginia program, the SSGN program, the Jimmy Carter program; I did the propulsion plant for Seawolf. I worked an extremely long time with no specs with naval reactors. The naval reactors tailor the requirements for the ship. The service combatants were not doing as much of this approach.
With Admiral McCoy, the Navy has essentially said that they are going back to the way we used to do it and that’s specifying the requirements based on the ship’s need. Not based on every Tom, Dick and Harry that are deciding well, I want this, I want that, I want this, I want that without any concern for cost.
There are other ways to skin the cat. And some of those are cheaper and much easier from the standpoint of building the ship, and buying and servicing the equipment. With that premise in mind, we began to focus on how we could reconfigure this ship to give the Navy great capability for a much-reduced price.
As we began to do this, we probably worked for a couple of weeks, three weeks, and then we sat right down with the Navy, and we began to iron out what is it you really want?
And what is it we might be able to leave at the pier side? We developed a good set of requirements against what could be affordable. What’s the minimum capability you want with the ship? And how can we design and build a ship, so that there is flexibility to add much capability later. This ship is actually, in my opinion, the Navy’s first truck.
Throughout the interview, Harris focused on the approach to building the ship.
And he highlighted three key elements to building on time and under cost.
The first was focus on process; the second on the opportunity to leverage a commercial program and the third to work with the South Koreans.
First, Harris highlighted what he sees as the key package of process elements central to success.
We combined 4 key elements to produce the ship. You have to design it right while you are looking at the manufacturing processes. When you get to the build cycle, you need to use state of the art processes. Before you build, you need to ensure that the material to build the ship is completely available. And you need skilled tradesmen to build the ship and to feel free to communicate changes they think need to be made to improve the build cycle.
In other words, you need a good design with good quality planning, material available and skilled tradesmen.
Secondly, the MLP is based on the foundation of an already built Arctic tanker, which NASSCO built for British Petroleum. The advantages of leveraging a previous commercial ship were important in many ways, but one crucial element was building a more maintainable ship.
This ship is as maintainable as any ship ever built. It has a lot of space, it’s wide open, it has good craneage and all the rest. The ship was originally a BP tanker; we built four of them. And we took the Navy with us, to visit the BP ships and asked them: what’s good about this ship? What’s bad? What would you change if you could change it?
And there was some things dealing with maintenance, for example, which they recommended ought to be changed. For example, in the engine room, there are overhead cranes to take the diesels apart and do service on the diesels. But what wasn’t there was temporary lay-down space when they needed to disassemble the engine for maintenance and repairs. They took a deck that we had put in and extended it about four feet.
We said that’s a good idea. So we took the whole deck of the MLP and extended it four feet.
Thirdly, Harris highlighted the role, which South Korea played in getting the build cycle right or to provide important inputs to state of the art production processes.
The Koreans have helped us immensely in the shipyard over the last seven years, not just for MLP, and not only in designing it but in how to build it. It is crucial to design it right the first time. As you’re getting into the build cycle, you need to make sure that the processes you’re using are state-of-the-art processes. And that’s always been an issue in this country. Sometimes we are too arrogant. We don’t recognize how qualified other countries of the world are in building world-class ships.
The Koreans and Japanese are the best shipbuilders in the world. We build about .2 percent of the tonnage in the world. The Koreans, Japanese and Chinese build the vast majority of the rest.
If you look at their approach, they never start a construction project without having their design done, the planning done and the material available. And what we sometimes miss in this country, there will be people who say I got 80 percent of the design done, I’m in good shape. And that’s mediocre at best. And I’ll tell you why because the last 20 percent of the design is the most difficult. And if you’re looking at where you’ll possibly have inconsistencies, errors in the design process, it’s in that last 20 percent.
In short, not only is the MLP part of the sea basing revolution, it is a lead ship in a continuing approach to build navy ships in a new manner.
For other stories on the USNS Montford Point see the following:
https://sldinfo.com/the-seabase-in-evolution-the-navys-new-mobile-landing-platform/
https://sldinfo.com/attending-the-christening-of-the-usns-montford-point/
https://sldinfo.com/the-christening-of-the-usns-montford-point/
https://sldinfo.com/anticipating-the-usns-montford-point-an-interview-with-admiral-buzby/
https://sldinfo.com/adding-capability-to-the-evolving-seabase-the-coming-of-the-usns-montford-point/