2012-07-18 By Kym Bergmann / Canberra
This article has been provided by our new partner, Asia Pacific Defence Reporter and is published with their permission.
The announcement that Australia would participate in the Joint Strike Fighter project was made almost exactly a decade ago on June 22, 2002. In another piece of symmetry, the Government’s contribution of $300 million to the System Design & Development phase is the same as the amount of work won so far by Australian industry on the aircraft since that time.
The key driver behind the selection of the F-35 – a decision ratified in 2009 with the announcement that RAAF would initially acquire 14 of the aircraft – is its contribution to combat capability. As the only 5th generation aircraft in series production, it has long been regarded by most analysts as the only realistic choice for Australia. However, another big selling point was the pitch to local industry that by becoming involved in a program of such vast size, the commercial benefits would be similarly enormous.
The results to date have been mixed. Certainly the $300 million figure is not to be sneezed at and in the longer term this number might reach billions of dollars. Here the operative phrase is “in the longer term” because as production of the JSF remains at modest annual levels – and might remain so for some time – it could take Australian industry many years to recoup the investments they have made.
Australian companies are involved in the following domains:
- Tooling (Marand, Broens, Hofmann Metaltec)
- Support equipment (Varley, Broens)
- Airframe Machined parts (Ferra, Lovitt, Levett)
- Electronic equipment chassis (TAE, AW Bell)
- Weapon adapters (Ferra )
- Actuators for LG and weapons bay doors (Goodrich, Rosebank)
- Composite panels (Quickstep)
- Vertical Tails (Marand)
- Engine Removal & Installation trailers (Marand)
- Engine parts (Levett)
- EW system components (BAES Aust)
- Training courseware (KBR)
- Cockpit Voice Recognition (Adacel)
- Radar Components (Micreo)
- Test Program Sets and Interface Test Adaptors (Partech Systems)
In broad terms, each Joint Strike Fighter is built up in four sections (five if you count the wings twice); each being the responsibility of a different entity: nose (Lockheed Martin); fuselage (Northrop Grumman); tail (BAE Systems); and, wings (Lockheed Martin). Another major component – the engine – comes from Pratt & Whitney. The Prime Contractor is Lockheed Martin.
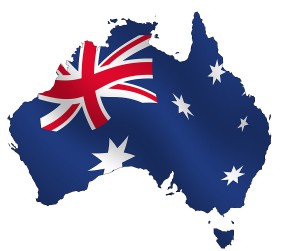
Because of the complexity of the aircraft and its tens of thousands of components and sub-assemblies, most Australian companies are working through Tier Two suppliers. In many cases, local companies are a second source of supply of components.
Several have been prepared to provide details of their involvement, though others seem reticent to make a comment. The Department of Defence has been prepared only to provide the above broad list.
The companies that have responded to requests for information are:
Brouens.
Broens Industries is a provider of innovative, precision engineered solutions, design, CNC machining, fabrication, and tooling.
Operating some of Australia’s largest and most advanced manufacturing facilities, Broens provides its services to Defence and many prime contractors in the Defence and Aerospace sectors locally and globally. Broens is also a supplier of Ground Support Equipment for RAAF and many other Air Forces around the world. In addition, Broens provides engineering equipment and services to other sectors including Automotive, Marine, Mining, Power, Rail, Automation and Renewable Energy sectors.
Broens was one of the first Australian companies to get involved in the Joint Strike Fighter Program, eight years ago. The introduction to the JSF prime and first tier companies was through the DMO and Department of Industry officials, followed by a series of inbound and outbound visits for Lockheed Martin, BAE Systems, and Pratt & Whitney.
Broens’ is doing a limited amount of work directly for Lockheed Martin including the current work, building Paint Cell Holding Fixtures (PCHF).
The majority of Broens’ JSF work however is for BAE Systems PLC, including the manufacture of Fixtures and Composite Tooling for the vertical tail of the F35 aircraft, which is being built by BAE Systems in the UK. As a result of the trust Broens earned, BAE Systems approved Broens to perform and sign-off on the quality inspection and qualification of tooling on behalf of BAE Systems.
Broens has also won an international multi-million dollar tender by Pratt & Whitney to design and manufacture an Engine Gearbox Lift for the Joint Strike Fighter. The first article of this device was delivered last year, and Broens was complimented on the ingenuity of the design and quality of manufacturing. Currently Broens is in the process of manufacturing multiple units of this device, and ultimately every JSF squadron around the world should have one or more units, with an estimated total of 150 Lifts.
Broens experience in Aerospace Composite Tooling is wider than the JSF program, including the design and manufacture of Composite Tooling and Layup Mandrels for Boeing Aero-Structures on the B737, B747, B757 and B777 programs and currently for the B787 Dream Liner. For Military aircraft, Broens’ work includes F/A18 Flap Tooling and C130J mandrels for composite ribs and Drilling Jigs.
Chemring
Chemring Australia is leading a significant element of Australia’s JSF industry participation through its program to manufacture air-launched expendable countermeasure flares for the JSF. The company recently became Australia’s first and only manufacturer of countermeasure flares with the successful commissioning of its new state of the art production facility in Lara, south west of Melbourne.
The company has invested $35 million in the facility that has been developed to produce to conventional MTV (Magnesium/Teflon/Viton) countermeasure flares of all configurations to satisfy the existing needs of the Royal Australian Air Force, and manufacture flares for the JSF without the need for major plant modification. This has been achieved by incorporating features into the facility design specifically for the JSF flare manufacturing process and maximising flexibility to enable incorporation of the additional JSF process requirements. Designed with operational safety as the key design parameter, the facility’s main production building is fully automated, negating the need for any operators to be exposed to those hazardous processes such as production of energetic materials.
Chemring Australia has been engaged with major stakeholders such as including the Defence Materiel Organisation’s JSF Defence Industry Team, federal and state governments, Lockheed Martin and BAE Systems over several years to mature the JSF flare production opportunity. In 2010 Chemring Australia received approval of a Manufacturing Licencing Agreement (MLA) by the US Government to be the second source manufacturer for the JSF flares. The MLA provides Chemring Australia with access to the technology and the authorisation to manufacture countermeasure flares for the global JSF fleet. Since late 2011 Chemring has been working closely with the US Navy Naval Air Systems Command (NAVAIR), the agency responsible for procurement of the JSF flares, on development of the detailed qualification plan. This plan will see Chemring Australia produce JSF flares for First Article inspection in 2014 and produce volume quantities to meet the introduction in to service dates for operators.
Further opportunities for Australian industry should develop through the supply of components for the JSF countermeasure flares. As the countermeasure flares are consumable items, flare manufacture will continue well beyond the completion of the JSF production, providing for a viable and sustainable long term Australian Industry Capability.
Lovitt
Lovitt Technologies Australia, established in 1954, is an Australian owned and operated SME specialist precision machining house with its core capability servicing the specific technical needs, volumes and schedules associated with Australian and International aerospace and defence programs. Lovitt Technologies Australia are participating in a number of Global Supply Chain initiatives which have the potential of providing Australian industry with exposure to larger product volumes associated with the full program requirements to supplement our direct negotiations with other Australian and international OEMs and prime contractors.
For the JSF F-35 Program the company has been involved since the early days of Australia’s selection of the aircraft, being a founding member of the Industry Capability Team (ICT) established by the Australian Government to support the Program and Australian Industry involvement in the manufacture and supply of product and services into Lockheed Martin Aeronautics, its partner organisations and systems suppliers. To achieve work from Global Supply Chain initiatives and other international programs such as the JSF F-35 Lovitt have needed to exhibit and prove not only “state-of-art” manufacturing facilities, technical ability and the mandatory ISO / AS Quality Certification but also internationally competitive pricing, usually expressed in $USD.
Being internationally competitive with the current strength of the $AUD against the $USD and other major currencies is a challenge for both military and commercial aerospace and defence projects. Lovitt Technologies Australia have achieved significant success in being awarded orders for the manufacture and supply of complex precision machined components and assemblies into the SDD and LRIP phases of the JSF F-35, including Long Term Agreements (LTAs) with Lockheed Martin and systems suppliers into the Program. We look to retain our status of a quality supplier into the Full Rate Production phases of JSF F-35. Similar long term contractual agreements have also been achieved for production requirements for Boeing and other aerospace and defence programs.
Our involvement in Global Supply Chain programs and long term agreements such as those with Lockheed Martin for the JSF F-35 Program and with Boeing for their military and commercial aircraft programs is a must to achieve the required volume of production hours into our manufacturing facility and to maintain the support of local sub-contractors providing treatments and services incorporated in the finished product to be supplied by Lovitt Technologies Australia.
Quickstep
In 2009, Quickstep signed Joint Strike Fighter (JSF) memoranda of understanding with Lockheed-Martin, Northrop Grumman and BAE Systems to become the sole Australian supplier of composite parts to what is widely regarded as the largest military aerospace program in the world. More recently, the company received approvals for the JSF Qualified Product Listing in 2011, followed by the initial two Long Term Agreements from Northrop Grumman. This program could generate revenues of up to $700 million for Quickstep over the next two decades.
In February 2012, Lockheed-Martin selected Quickstep to manufacture carbon fibre wing flaps for the C130-J Hercules aircraft worth up to $100 million over 5 years.
Besides the aforementioned giants of the aerospace industry, Quickstep is also partnering with other leading aerospace, automotive and defence organisations, such as the US Department of Defense, Airbus, Eurocopter, Sikorsky, Audi and Lamborghini .
So, what drives these companies to work with Quickstep?
Firstly, Quickstep’s patented “liquid curing” is a highly competitive solution for manufacturing of lightweight composites for aerospace, automotive or armour composite parts. The company has both traditional and proprietary composite curing technologies and is AS 9100 compliant.
Secondly, the company has highly-regarded expertise as well competitive prices in the production of aerospace-grade composite components.
Thirdly, Quickstep has an international presence through process development subsidiaries in Dayton, Ohio, and Ottobrunn, Germany and an alliance with Deakin University in Geelong, Victoria.
Fourthly, the Australian Department of Defence strongly encourages foreign OEM they buy from to integrate Australian companies in their supply chains.
TAE
TAE Gas Turbines Pty Ltd (trading as TAE) has a multifaceted involvement in the F-35 program. A large part of this involvement is in relation to the planned sustainment of the F-135 engine that powers the F-35. As Australia’s premier military turbine engine maintenance repair and overhaul (MRO) business, TAE has had a long relationship with Pratt & Whitney, a relationship it plans to continue with the F-135 engine both for the Royal Australian Air Force (RAAF) and potentially for regional operators through out the Asia-Pacific. In addition to TAE’s core MRO capability, it is the long proven engineering and air worthiness management experience that TAE offers that is of especial interest to both Pratt & Whitney as well as operators.
In a related field, TAE has been working in conjunction with Vipac Engineers & Scientists and Pratt & Whitney to develop advanced new engine monitoring technologies that will also hopefully have a role within the F-35 Program and especially in support of the F-135.
Finally, TAE’s manufacturing division has been producing components for the F-35. These components are centred upon TAE’s award winning Aluminium Vacuum Brazing technology. TAE is the first Australian company to develop this technology and one of only a very small number world-wide able to offer the capability.
Developed over the past four years, this technology is used in areas such as liquid-cooled electronics enclosures, cold plates, heat exchangers, wave guides and radar assemblies. This technology is also supported by TAE’s associated capabilities such as precision machining, heat treatment, chromate conversion coating, painting, component assembly and any required proof pressure testing and/or flow testing. In addition to its manufacturing capabilities, TAE also has the capability to assist in the design and prototyping of components utilising this process, something that is already finding interest within the F-35 program.
In recent years TAE has won production contracts and signed long term agreements from international multi-national aerospace companies such as Harris Corporation and BAE Systems. Included among these contracts have been situations where TAE is now the sole, global supplier for complex liquid cooled components on the F-35.
TAE is now engaging with companies such as Moog Inc, Northrop Grumman, Hamilton Sundstrand and Cobham Systems for other F-35 components and hopes to sign further contracts with these companies in the near future.
Other companies.
Another major participant is BAE Systems Australia. During a recent visit to Adelaide organised by the State Government, APDR was shown the company’s titanium milling facility that will be producing the vertical tails of the aircraft. Two milling machines are already in operation – having cost around $10 million – and an even larger one will arrive from Switzerland later this year for another $10 million. It took some time to arrange an Australian company willing to make this sort of investment and discussions with a number of companies proved fruitless until BAE Systems were prepared to step up to the plate.
Of the other companies involved, the one with potentially the most lucrative chunk is Ferra, which produces the weapons adopters within the aircraft’s internal station. However, like many other participants in the JSF build, cash will only really start to flow once the JSF enters full rate production – and that is still several years away.
For a look at the global supply chain, including the United States, please look at the rotator on the main page of the F-35 consortium, notably the slide show on the second panel of the rotator.
For a PDF of this article go to this link
Download Your Copy of Australian Defense Industry and the F-35
And for a report examining the evolution of the Australian defense market through 2017.